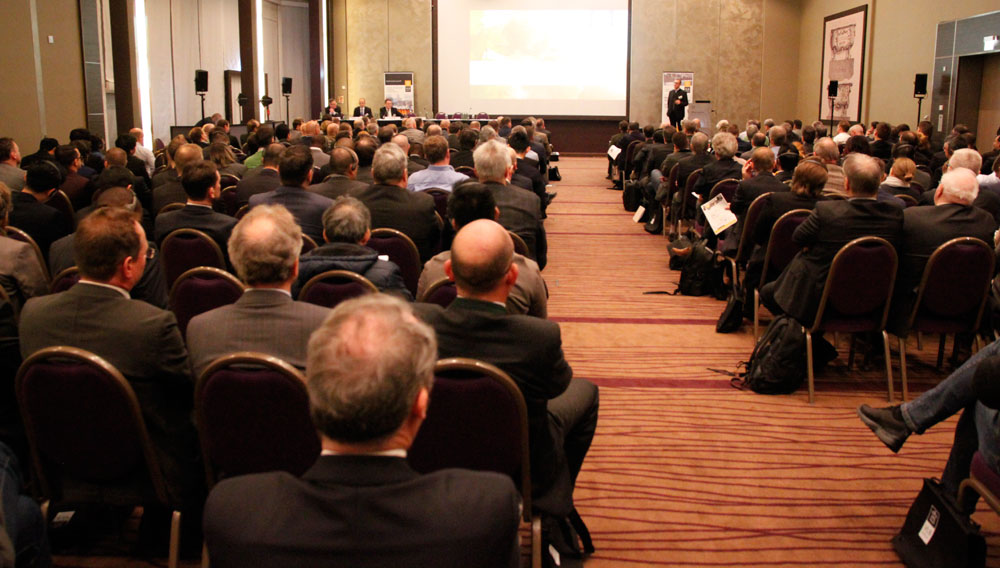
Die 104. Brau- und maschinentechnische Arbeitstagung der VLB Berlin vom 6. bis 8. März 2017 hatte in diesem Jahr zwei Gesichter: Das eine, in dessen Augen ganz deutlich das Paulaner-Zeichen leuchtete, haben wir in der letzten Ausgabe der BRAUWELT bereits beschrieben (BRAUWELT Nr. 11/2017, Seite 297). Am zweiten Veranstaltungstag drückte wiederum besonders eine Sache der Veranstaltung ihren Stempel auf: Nessie.
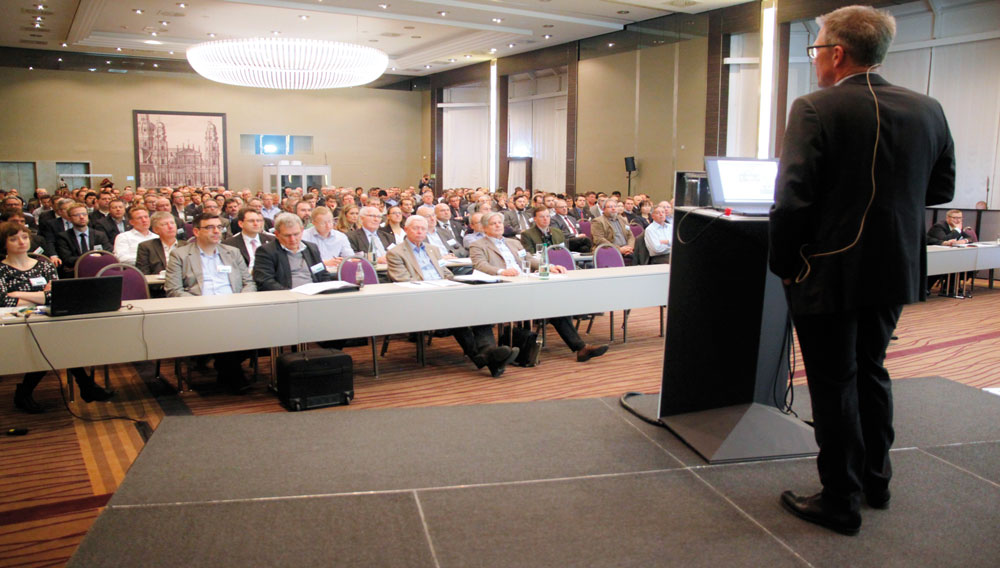
Ein Greenfield-Projekt in solchen Dimensionen – da ist einem die Aufmerksamkeit der Branche sicher: Rund 300 Mio EUR hat der Neubau der Paulaner Brauerei Gruppe GmbH & Co. KGaA in München-Langwied wohl gekostet. Nach, wie man hörte, einigen Startschwierigkeiten, angesichts eines so großen Projekts kaum verwunderlich, läuft die Brauerei im Autobahndreieck zwischen A8 und A9 langsam runder und die Verantwortlichen werden zeigefreudig. So stand die VLB Frühjahrstagung vom 6. bis 8. März ganz im Zeichen der neuen Brauerei. Das Tagungsprogramm widmete sich am ersten Tag komplett dem Neubau in Langwied. Das gab uns die Möglichkeit, einen guten Überblick zu erlangen, worin die 300 Mio EUR nun versenkt wurden, und im Folgenden einen kompakten Eindruck zu vermitteln.
Der Rohstoff Hopfen trägt wesentlich zur mikrobiologischen Stabilität von Bier bei. Im vorliegenden Beitrag wird die Ermittlung einer sogenannten hopfenbasierten Hemmkraft zur Einschätzung des antimikrobiellen Potentials von Bier beschrieben, die in Teil 2 durch Praxisuntersuchungen verifiziert wird.
Nicht nur Hopfen und Malz müssen erhalten werden, sondern auch das Wissen, wie diese aufbereitet und verwertet werden.
Um neue Rezepturen für kaltgehopfte Biere zu entwickeln, führen viele Brauer zunächst Versuche im Kleinmaßstab durch. Die Kalthopfung in Fässern bietet den Vorteil, dass der Brauer mit wenig Bier- und Hopfenmenge viele Kalthopfungsvariationen – beispielsweise unterschiedliche Biersorten, unterschiedliche Hopfensorten oder auch unterschiedliche Kontaktzeiten – testen kann, um ein sensorisch ansprechendes Rezept zu kreieren. Anschließend wird dieses Rezept meist unverändert in den Industriemaßstab übertragen. Ob Biere nach der Kalthopfung in unterschiedlichen Maßstäben auch wirklich sensorisch und analytisch vergleichbar sind, war Gegenstand der hier dargestellten Untersuchungen [1].
Angeregt durch jüngste Entwicklungen im Sudhausbereich, insbesondere der Maischefiltration (siehe BRAUWELT Nr. 6, 2017, S. 139-142: „Neues Verfahren der Maischefiltration“), wurde die Bedeutung der Jodnormalität von Bierwürzen für die Beurteilung der Sudhausarbeit zusammenfassend analysiert und bewertet.
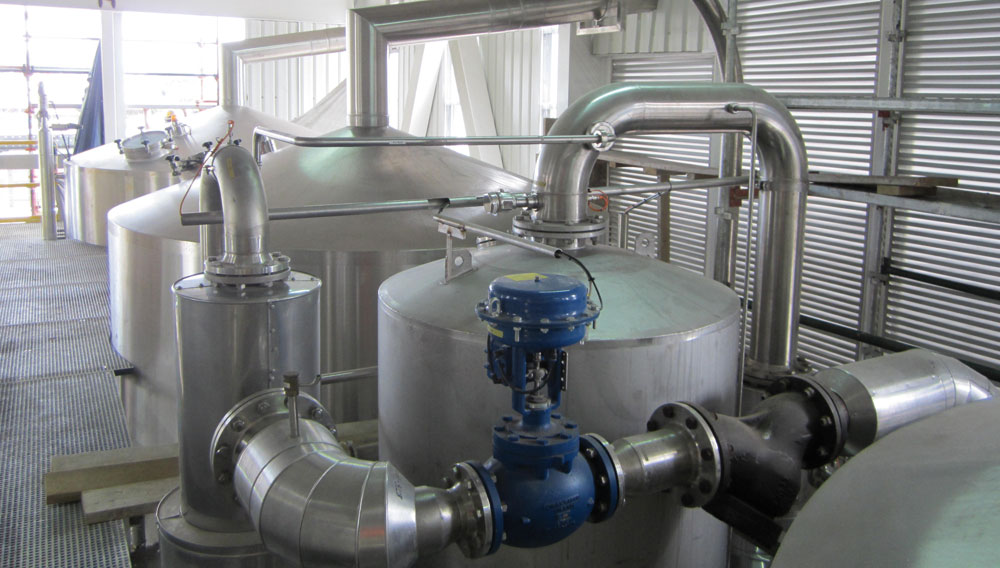
Die Brauerei Paradise Beverages (Fiji) Limited mit Sitz in Suva, Fidschi, war ursprünglich Teil der Foster‘s Group Pacific Limited. Sie änderte ihren Namen 2012, als sie zum Unternehmen der Coca-Cola Amatil (Fiji) Limited wurde. Derzeit produziert die 1957 gegründete Brauerei jährlich etwa 100 000 hl. Die Hauptsorte Fiji Gold, ein helles Lagerbier mit 4,6 Vol-% Alkohol, hat daran einen Anteil von circa 60 Prozent. Neben der schrittweisen Erneuerung der Produktionsanlagen für die verkaufsfertigen Biere ist die Einrichtung einer High-Gravity-Schiene das jüngste Projekt der Brauerei.
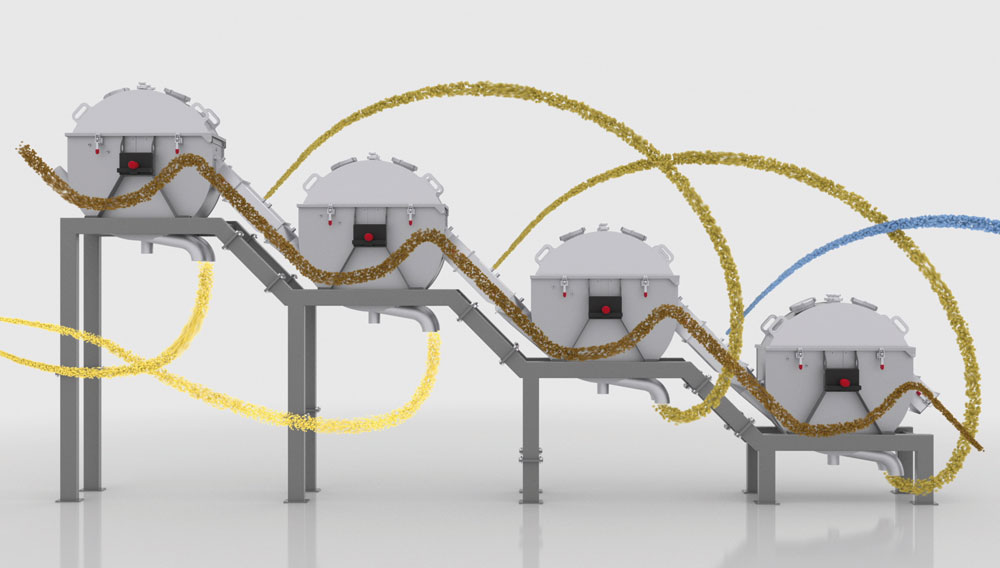
Kontinuierlich | Mit Nessie by Ziemann® wurde auf der BrauBeviale 2016 in Nürnberg ein in der Bierherstellung neuartiger Läuterapparat präsentiert, der die klassische Sudhausarbeit nachhaltig verändern soll. Die BRAUWELT wird diese Technologie in einer Artikelserie unter allen relevanten Gesichtspunkten vorstellen. Teil 1 beschreibt die Entwicklungsziele, das eigentliche Verfahren und den apparativen Aufbau. In folgenden Beiträgen werden die technologischen Effekte auf das Läutern sowie weitere Entwicklungen für die vor- und nachgelagerten Prozessschritte vorgestellt.
Bei der Entwicklung von Kleinbrauereien werden üblicherweise die in Großbrauereien bewährten Systeme auf einen kleineren Maßstab heruntergebrochen. Das hier vorgestellte patentierte Sudhauskonzept verfolgt einen anderen Ansatz zur Realisierung eines einfachen, flexiblen und effizienten Systems für Sudhausgrößen von ca. fünf bis 50 Hektoliter pro Sud.
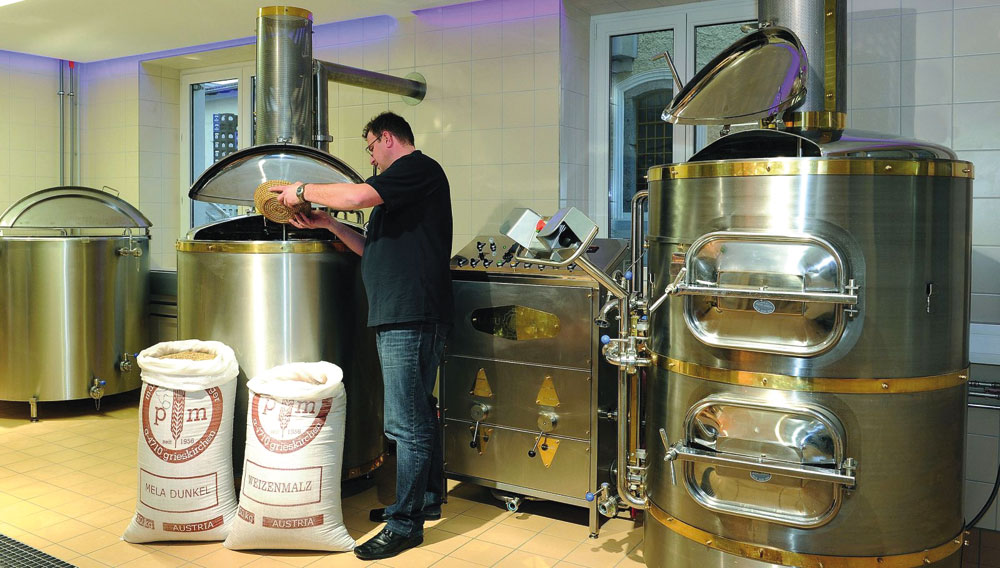
Klein- oder Pilotanlagen werden sehr erfolgreich in mittelständischen Brauereien eingesetzt und bringen den Unternehmen klare Wettbewerbsvorteile. Die Entwicklung neuer Rezepte, die Produktion ausgefallener Sorten für den Craft Bier-Markt, Events zur Kundenbindung, wie z. B. die Abhaltung von Braukursen, sowie interne Schulungsmaßnahmen für die Mitarbeiter lassen sich mit einer Kleinbrauanlage optimal durchführen. Die professionelle Brauwirtschaft verlangt dabei von Brauanlagenherstellern sehr hohe Standards in Bezug auf Qualität, Effizienz und Prozesstechnik.
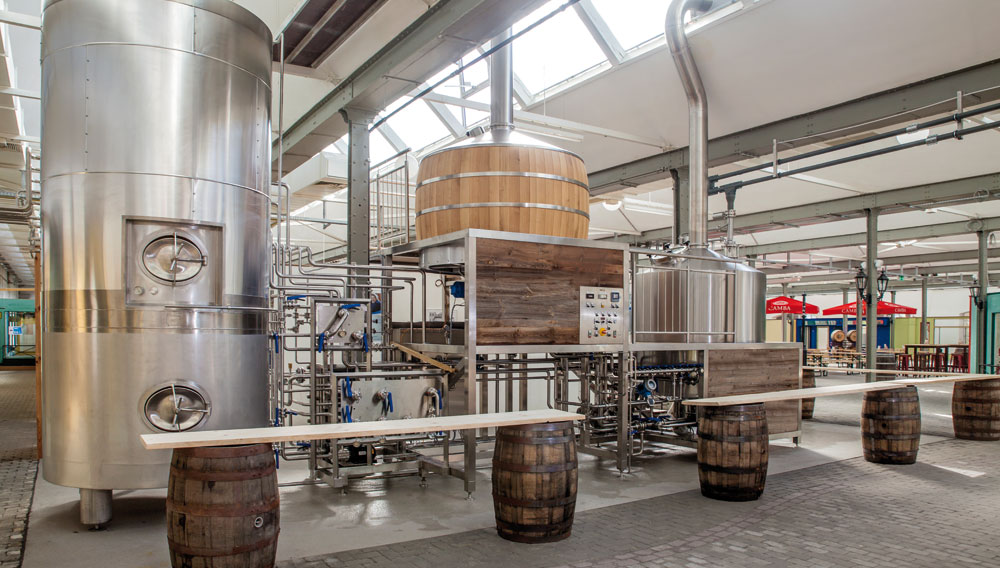
Das Sudhaus ist das Allerheiligste jeder Brauerei, geöffnet werden die Sudkessel in der Regel nur für die eigenen Biere. So mancher Brauer lässt für einen Collaboration Sud den einen oder anderen Kollegen mitmischen. Aber das eigene Sudhaus für andere Brauer bzw. Brauereien öffnen, vielleicht sogar für die Konkurrenz? Das ist für die meisten Brauereien in Deutschland unvorstellbar – in Gundelfingen gibt es aber seit 2015 eine Brauerei, die genau das tut: die Camba Old Factory GmbH öffnet ihr nagelneues 20-hl-Sudhaus für Brauer, die keine eigenen Anlagen zur Verfügung haben.
Über sieben Tonnen Edelstahl: So viel wiegen die drei neuen Gefäße, die im Dezember 2016 ins Sudhaus der Störtebeker Braumanufaktur gehoben wurden. Eine zusätzliche Maischepfanne, ein Läuterbottich und ein Würzevorlaufgefäß ergänzen nun diesen Teil der Brauerei.
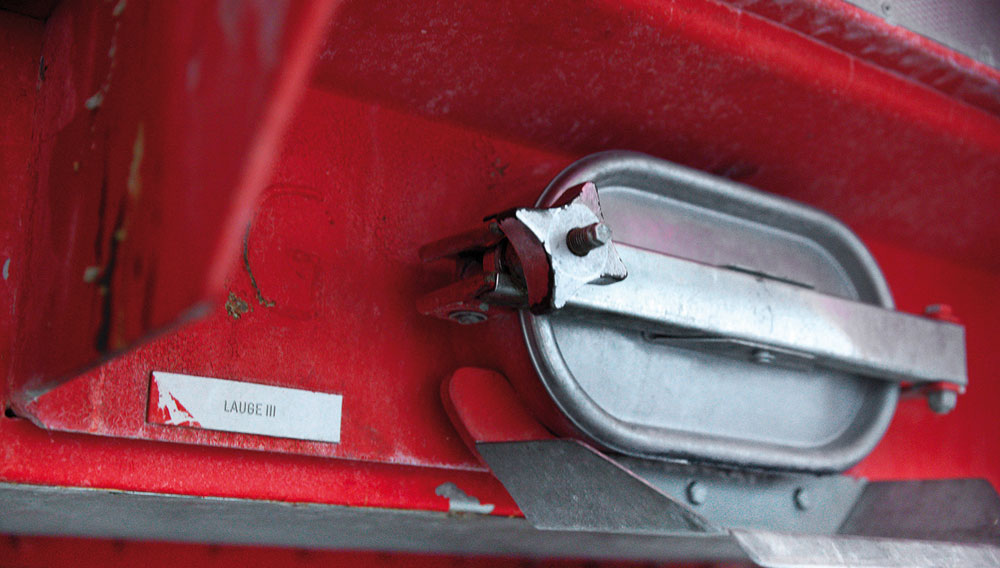
Immer wieder werden der Berufsgenossenschaft Nahrungsmittel und Gastgewerbe (BGN) Unfälle an Flaschenwaschmaschinen oder Zellenradschleusen gemeldet. Gefahren bei Routineaufgaben wie Reinigung, Wartung oder Probenahme werden dabei häufig zu sehr auf die leichte Schulter genommen, die entsprechende Schutzkleidung kommt, auch wenn vorhanden, nicht zum Einsatz. Die konstruktiven Lösungen vor Ort sind häufig nicht ideal gewählt und im schlechtesten Fall ist das Personal nicht entsprechend auf mögliche Gefahren hingewiesen oder ausgebildet.
Ohne eine Aufnahme von Messwerten und Daten bei produktionstechnischen Prozessen kann es keine Automatisierung geben. Diese Tatsache wird jedem Besucher klar, der dem Trend zur Digitalisierung und Industrie 4.0 folgt, die auch vor der Getränkeindustrie nicht Halt machen wird. Ein Messerundgang auf der SPS/IPC/DRIVES 2016 in Nürnberg sorgte für Einblick.