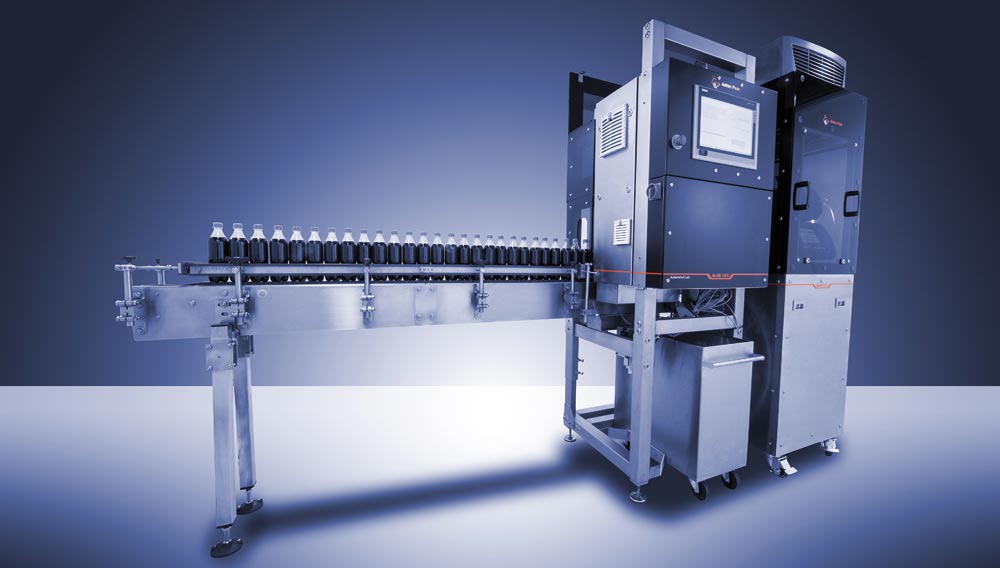
Inline and fully automated | Conventional quality control carried out in the laboratories of breweries and beverage producers is usually performed manually and requires a significant amount of time and labor. With the automation solutions available from Anton Paar, the laboratory is located directly on the production line.
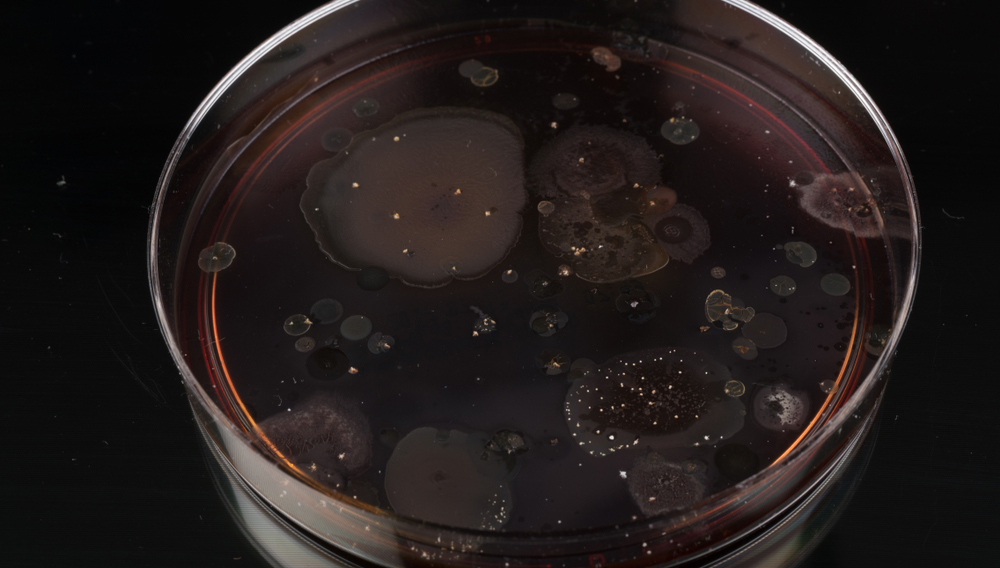
Optimising evidence | Detection of beer-spoilage bacteria in the brewing process is of the utmost importance. These bacteria can cause, among other things, hazes, acid and off-flavours in the product. It is extremely difficult, especially in pure culture yeast and also in cropped yeast, to track down these beer spoilers because their growth is suppressed by yeast. In addition, these bacteria are often present as trace contaminants in such yeast. In this study, a method has been developed to detect beer-spoilage bacteria in pure culture yeast much faster and with a higher degree of reliability than has been the case with existing methods.
Establishing a measurement methodology | The arabinoxylan substance group has been hitherto largely disregarded in the area of beverage analyses and interpretation of technological repercussions, this is due in part to the limited availability of measurement methodology. However, it is a cell wall component that should not be underestimated and is possibly – in addition to β-glucans – another important indicator or technical parameter for cytolysis.
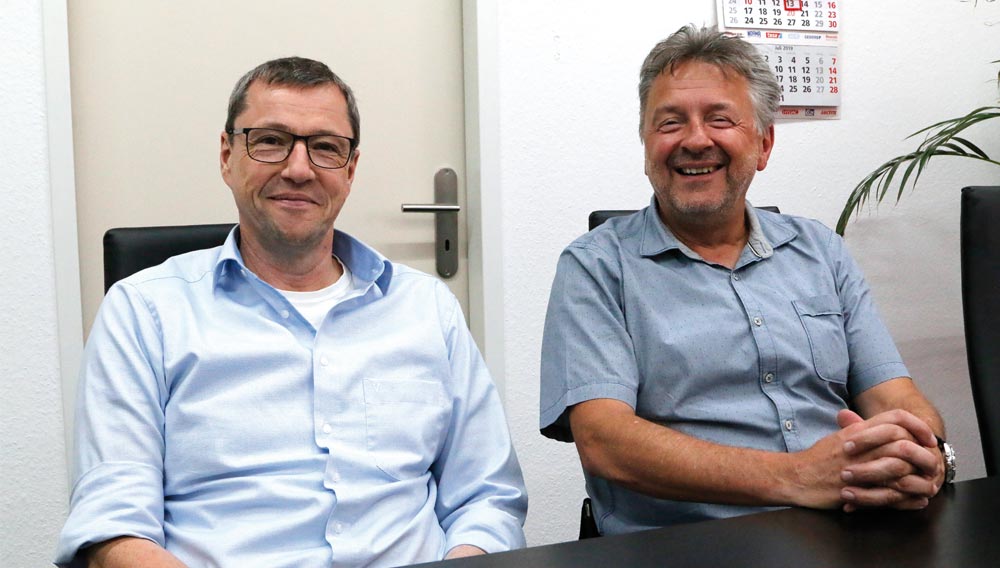
Professional exchange | Johann Angres, Managing Director of Steinfurth Messsysteme in Essen, Germany, received a great honor in April of 2019. He is the first German ever to be elected to the board of the ISBT. Never heard of the ISBT? The International Society of Beverage Technologists is the MEBAK or EBC of the soft drink industry. And because we also were not familiar with the ISBT, we decided to visit Johann Angres in Bochum to find out more about the association, his appointment to the board and the changes currently taking place at his company.
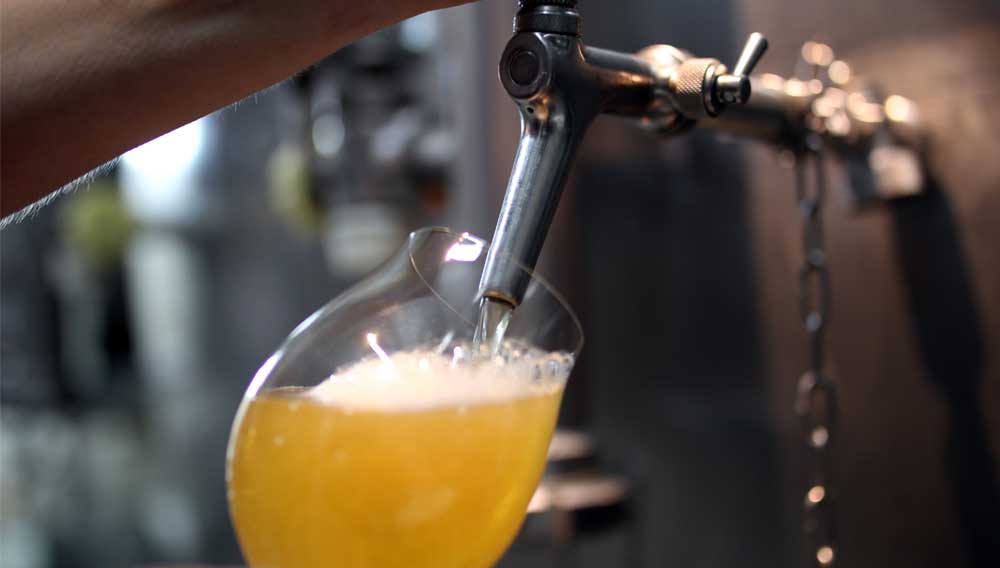
Indispensable knowledge | Time and again, one sees a server behind a bar who finds it impossible to fill glasses with draft beer at a satisfactory tempo, even though the dispensing system is apparently adjusted perfectly. The oft discussed saturation pressure is of course critical, as is the temperature of the beer. However, other factors are frequently not taken into consideration and these will be more closely examined in this article.
Non-alcoholic beers | The number of non-alcoholic beers acknowledged as being isotonic is steadily rising. Non-alcoholic beer-based beverages such as shandies are meantime on the shelves. Isotonic beverages are liquids with osmotically active particles per kg, the number of which corresponds to human blood. Size or type of particles does not play any part in osmotic pressure as these are not a chemical phenomenon but a physical one. The number of particles (dissolved atoms and ions and also molecules such as sugar, proteins, ethanol) is solely significant. Thus, osmotic pressure is a colligative property.
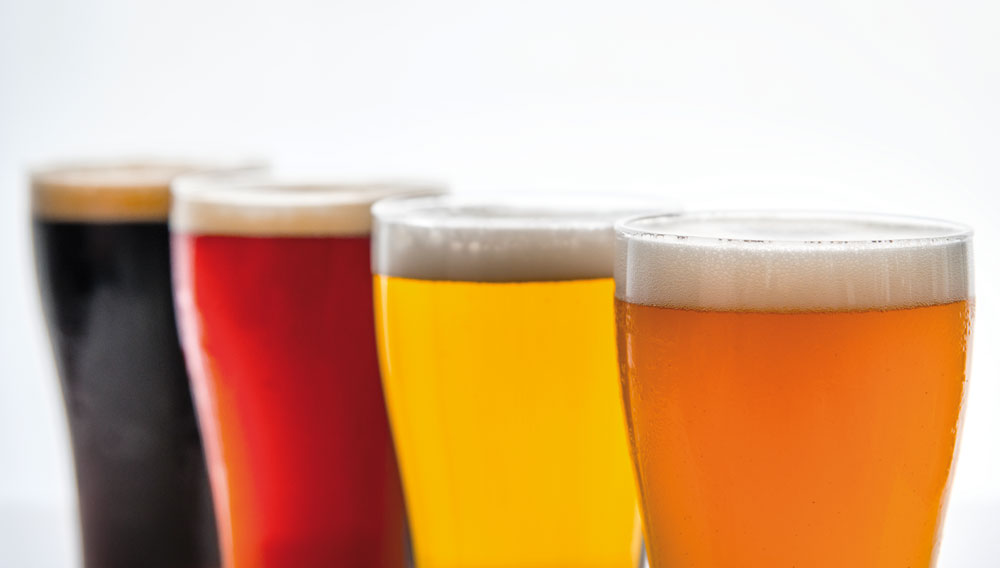
Quality assurance | Naturally cloudy beers such as Hefeweizen or unfiltered Kellerbier are a pleasure to drink. However, brewers attempt to obtain the clearest possible appearance of the beverage for most beer types. Consumers regard haze, e.g. flocculated proteins, as a quality flaw or as a sign of spoilage in many instances. This article describes ways in which turbidity measurement and quality assurance are handled successfully, even in dark beers.
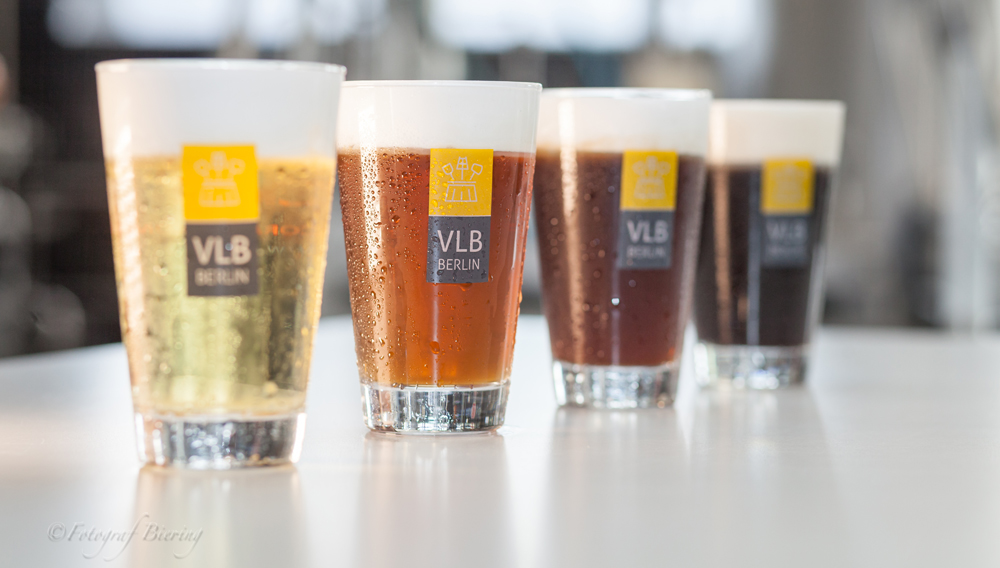
Statistically significant | This second contribution to sensory analysis in the beverage industry focusses on relevant factors and requirements that have to be taken into consideration and applied in order to obtain statistically significant results. In accordance with the test concept of the analysis method, the particular taster panel has to be evaluated. An effective method is set out by way of example. This is used to verify the robustness of sensory data collected and to map the range of sensory attributes of a product.
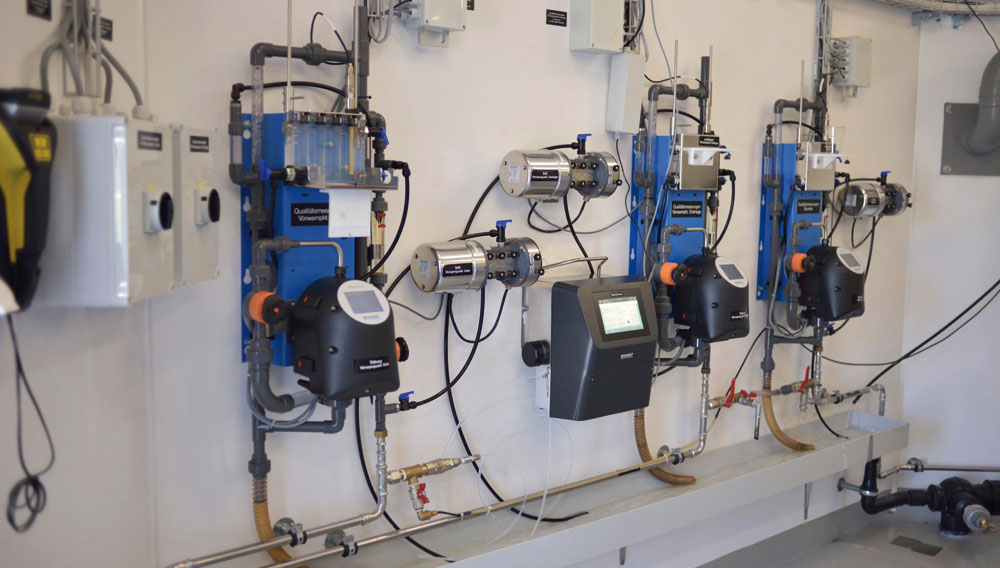
Flow cytometry | The risk of primary and secondary infection in beverages can be reduced if a beverage production facility is clean at all times and in all areas. Ensuring this is one of the central and cost-intensive tasks of beverage production. But how can you be sure that all pipes and equipment are always clean? How can this be monitored almost in real time?
Genetic test | Some contaminant yeasts make beer bottles and cans explode. Apart from being dangerous for consumers these ‘diastatic’ yeasts also cause loss of beer batches due to off-flavours, increased alcohol and over-carbonation in products. VTT scientists developed a genetic test for brewers to detect the strains that cause these problems.
Pilot tests | Part 1 of this contribution (see BRAUWELT International No. 2, 2019, pp. 144-147) reported about tests with mash and wort on a laboratory scale in which precipitation of prooxidative iron ions using hop α-acids in the form of CO2 extract additions was investigated. Part 2 deals with optimised hopping in order to trigger systematic precipitation of hop irons during brewing and thus extend the shelf life of beer.