Many different technical solutions for improving the environmental performance in a brewery are widely available from the major brewhouse suppliers. In part 1 of this series, the combination of a vapour condenser, condensate cooler, heat storage tank (stratification tank) and wort preheater was discussed. This is the obvious choice for any new brewery for recovery and reuse of thermal energy, even though this solution is not always a guarantee that energy is effectively recovered and reused. Often there is an imbalance between heat recovery and heat reuse. In spite of the benefits, surprisingly few breweries use stratification tanks.
Energy-conscious brewing | Energy efficient practices in microbreweries and brewpubs reach a limit very rapidly due to the small volumes they produce. After a batch is brewed, a volume of hot brewing liquor correspondent to that of the cast-out wort is generated through the process of wort chilling, for which there is no practical use. This is where the principles of low-energy brewing can be applied. The brewing equipment is heated using a buffer tank filled with hot water from the heating system, and at the end of the brewing process, all of the thermal energy is returned to the heating system, where it can be utilized for other heating purposes.
With the Filtech Show taking place from 24-26 February 2015 the City of Cologne in Germany will turn into a meeting place for all those involved with filtration and separation and adjacent sectors.
The brewing process is inherently energy and water intensive. In the second part of this publication, the process parameters that affect environmental performance in the brewhouse and cellar sections are analysed in order to provide brewers with some guidance when they evaluate proposals for energy and water saving projects. The boiler house, cooling equipment and water treatment units are not included in this study because these topics are extensively covered already in other publications.
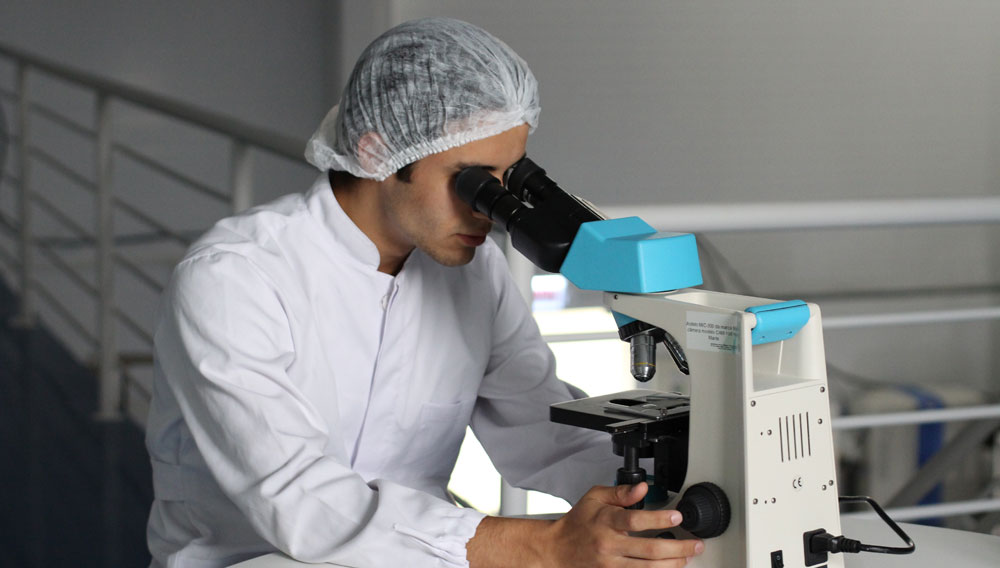
All over the world, manufacturers are under increasing pressure to manage natural resources in a responsible manner. This applies also to the brewing industry. Since most processes in a brewery are carried out batch-wise, energy and water recovery and reuse in a brewery is complicated though this is becoming more widespread now. In this first part of the publication, the brewhouse and cellar processes are mapped with the aim of calculating real brewery requirements for heating, cooling and fresh water usage in each step of the process. This flow sheet can then be optimised to lower overall water and energy consumption.
The 11th “Trends in Brewing” symposium is planned for April 13-17, 2014 and this year’s slogan is “Can Trends in Brewing be Revolutionary?” Organizers KAHO Sint-Lieven (KU Leuven), Ghent/Belgium, Heriot-Watt University, Edinburgh/UK, and the TU Berlin are hoping to recreate the resounding success of the previous event this year as well. The “trends” presented at the 2012 symposium attracted 360 industry representatives from a total of 24 nations to Flanders, where they met to discuss developments in brewing and malting technology.
BRAUWELT International congratulates Prof. Ing. Gabriela Basařová, DrSc. on her 80th birthday. Basařová was born on January 17, 1934 in Plzeň to a family of teachers. She graduated from secondary school in Plzeň and Institute of Chemical Technology in Prague, where she studied malting and beer brewing at the Department of Fermentation Chemistry and Technology. After graduating in 1957, she joined Plzeňské Pivovary, where she headed the control and research laboratories.
With the Eco vacuum pump KHS can already help the brewing industry to save almost 100 % water compared to the classic water ring pump. The new KHS Eco+ vacuum pump – or rather, the newly designed KHS Eco+ module integrated into the Eco vacuum pump – now has the added benefit that classic coolants for water recooling are now a thing of the past. This means that customers no longer have to invest in piping for coolant transfer which is often complex and costly.
From May 26th to 30th 2013, brewing scientists in Europe will converge on Luxembourg at the EBC congress. For the first time in the long history of the EBC, it will be held in this small country bordering Belgium, France and Germany. Luxembourg is a country with much to offer, as brewers will undoubtedly find out in May. We spoke with EBC president Dr. Stefan Lustig about what awaits those attending the Congress.
The European Brewery Convention (EBC) in Brussels is much more than merely the organiser of a biennial scientific congress in one of the member countries. The EBC is the technical and scientific arm of “The Brewers of Europe”, the umbrella organisation of the European Brewers’ Associations, and acts for them in an advisory and supporting function. After a three-year term in office, the posts of both EBC President as well as Vice-President were up for election.
In part I of this contribution (BRAUWELT International no. 5 2011, pp. 290-292), possible strategies for therecovery of water and recyclables in breweries were summarized. As a sequel, part II deals with effluent end-of-pipe treatment and elaborates on the solution that may ultimately prove to be the best for an existing brewery, taking account of considerations having a bearing on industrial water recovery. Solid recyclables, such as beer spent grains or yeasts, also have a high material and energy potential. Therefore, possibilities of recycling same are discussed, leaving aside agricultural use. This will become part of a future holistic concept.
Water is the most important raw material of the beverage industry – and clean drinking water is an increasingly valuable good. Apart from the economic responsibility, our industry has, therefore, also a major social responsibility to protect this vital resource. Efficient and sustainable water management requires an integrative approach, which taps the entire optimization potential around water usage. This includes the evaluation of local water catchment areas as well as the reduction of water consumption and the full recycling of any wastewater arising.