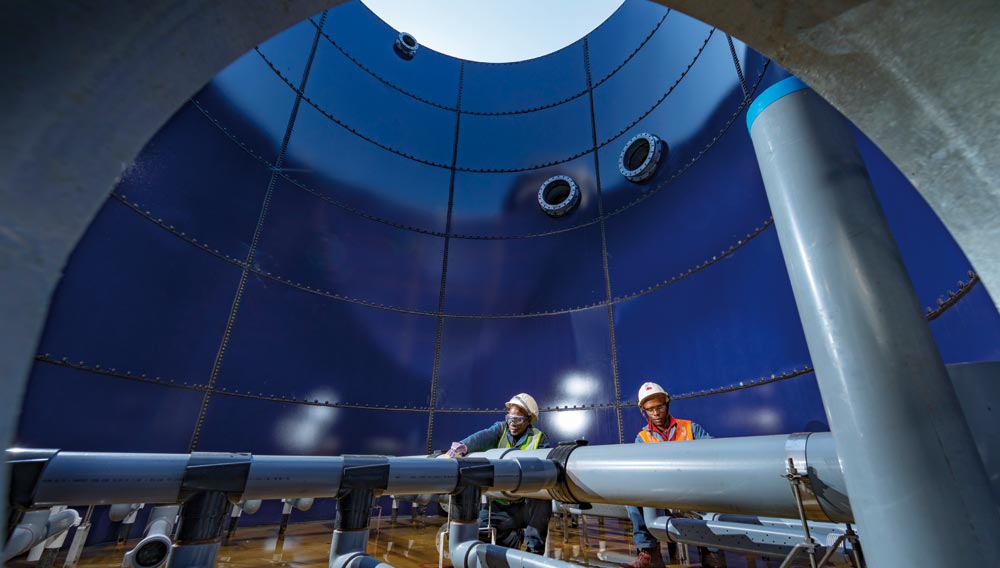
SME compatible | The Bavarian Karmeliten Brewery in Straubing is the first German brewery to decide on a turnkey installation of a fully biological treatment plant. The carrier-based system combining anaerobic and aerobic wastewater treatment of the Dutch company Aqana completes the energy/environmental sustainability concept of a CO2 neutral brewery that has won several awards. It has been grant-aided by the German Federal Government.
USA | The Supreme Court will hear arguments in November in a major environment case concerning the Clean Water Act. Sixty craft breweries have clubbed together over the summer and told the justices in a brief that weakening the federal regulation would damage their businesses.
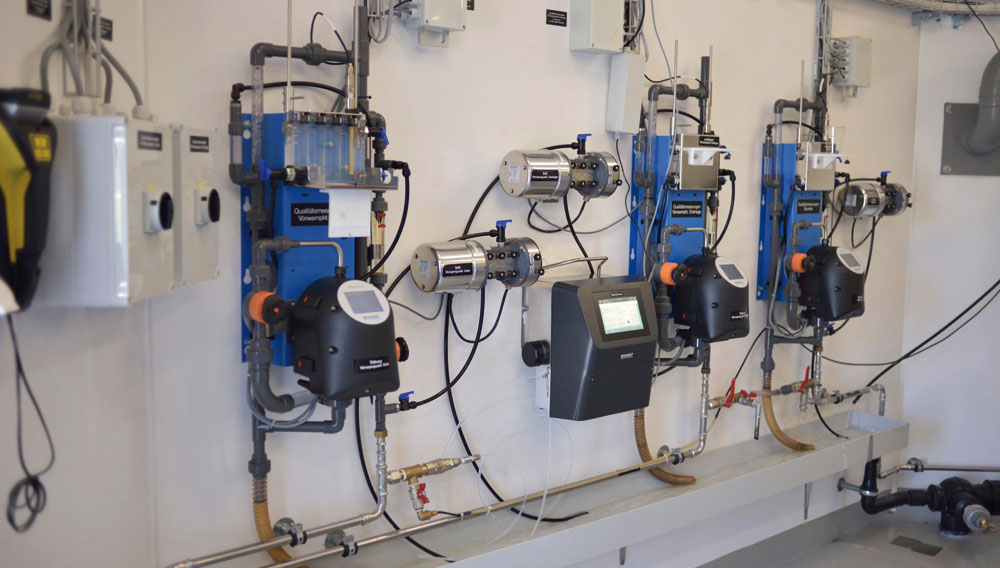
Flow cytometry | The risk of primary and secondary infection in beverages can be reduced if a beverage production facility is clean at all times and in all areas. Ensuring this is one of the central and cost-intensive tasks of beverage production. But how can you be sure that all pipes and equipment are always clean? How can this be monitored almost in real time?
Tool for process water treatment | In 1972, Karl Diether Esser presented his membrane filter test for evaluating filterability of beer [1]. At that time, it was important to identify beer with poor filtration properties as simply and early as possible. The question arises today whether the Esser test could also be used nowadays as a valuable tool for applications above and beyond beer filtration.
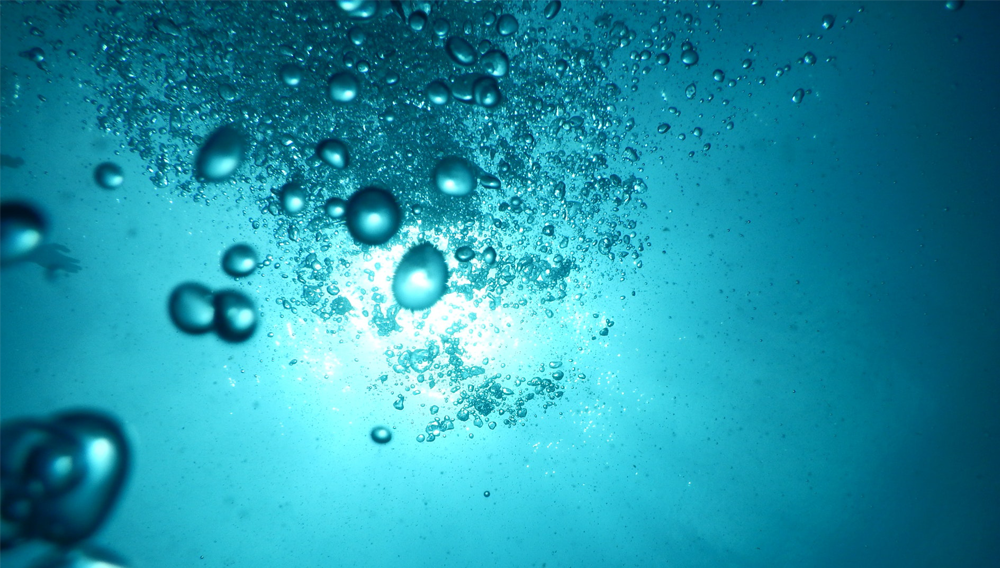
Water and energy savings | When preparing a reliable and up-to-date demand forecast, it is possible to operate machinery and plants in the utility supply section, reducing fluctuations and thus making it more efficient. This presupposes that the equipment has a wide operating range. This dual approach has been adapted in a cooperation project supported by Deutsche Bundesstiftung Umwelt (DBU – German Federal Foundation for the Environment) and implemented using brewing liquor and process water treatment with the help of a reverse osmosis plant as an example. The main results are presented below.
Promising technology | The Life-ANSWER project (Advanced Nutrient Solutions With Electrochemical Recovery) aims to provide an innovative technology that integrates electrocoagulation and microbial electrochemistry for treatment of wastewater originating from the agri-food industry. The ANSWER system makes it possible to reuse the treated water, producing enriched biogas (CH4 + H2) and fertiliser from wastewater.
New aerobic system design | The impact of environmental matters on business performance in the food and beverage industry is becoming greater and will continue to do so. In the dynamic field of food and beverage wastewater treatment growing numbers of new systems have been tested over the past decades. Aqana-Aqwise, an Israeli-Dutch joint venture has been increasingly successful with a reliable, ingeniously simple, very efficient and robust solution for handling these industries’ effluents.
Committed to sustainability | The impact of environmental matters on business performance in the food and beverage industry is increasing and will continue to do so. In the dynamic field of food and beverage wastewater treatment increasing numbers of new systems have been tested over the past decades. Aqana-Aqwise, an Israeli-Dutch joint venture has been increasingly successful with a reliable, ingeniously simple, very efficient and robust solution for handling these industries’ effluents.
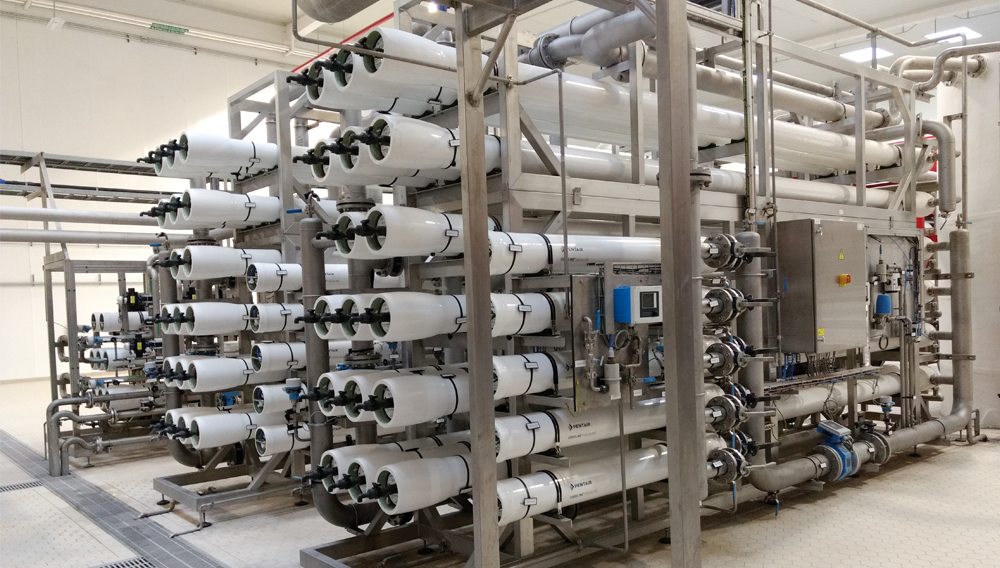
Reducing the water footprint | Breweries have been amongst the pioneers in sustainable use of natural resources. Apart from quantity, water quality is also a continuous reason for concern. Sourcing top quality brewing water in arid regions implies membrane based solutions allowing removing undesired constituents as well as maximal water recovery.
Water crisis | A few weeks ago marked the tenth anniversary of the financial crisis that sparked a sharp escalation in the cost of credit for banks, created a panic in financial markets, and led directly to all the other tumultuous events of the following year that cost tens of billions of euros. Much has since been written about the crisis of 2007 and whether lessons have been learned. Why were so many early warning signs ignored? One of the key learnings is a renewed focus on “stress testing”.
Water Degasification 2.0 | Degasification has become a widely established process unit operation for water treatment in the brewing and beverage industry. Depending on the particular industrial sector and use of degassed water, residual oxygen levels below 10 ppb are required. Use of a stripping gas, mainly CO2, in rare cases N2, is usual practice in all processes generally used in the beverage industry. Thanks to a new technology developed by corosys, no stripping gas and no thermal energy or chemicals are required. According to the company, the same low residual oxygen concentrations as in the most effective conventional processes are achieved.
Experience over a five-year period of full throughput using anaerobic co-digestion of brewery yeast for biogas production is described in this contribution. The brewery, with a total amount of available yeast (0.7 v/v %), had a 26.2 % increase in COD load and a 38.5 % increase in biogas production resulting in an increase in the biomethane/natural gas substitution ratio in the brewery from 10 % to 16 %.