The relevance of brewing liquor for beer quality is often underestimated and its quality is often disregarded or ignored, even though the finished product beer consists of 90 - 92 percent water.
In Mid-october, 8 speakers from the department of research for engineering sciences for food products and biogenetic raw materials and the research center for brewing- and food quality, Weihenstephan organized a seminar for 80 participants at El Salvador featuring the latest results of research at Weihenstephan.
According to the Drinking Water Ordinance “water for human consumption” is understood as “drinking water” and as “water for the food industry”. To simplify matters this paper uses the term “drinking water”. It was realised early that the supply of the public with clean drinking water is extremely important. Hereby, the microbiological property plays an essential role.
For more than 30 years the Institute Romeis Bad Kissingen, Oberthulba, Germany, has been successfully active in the field of up-to-date production technologies, product quality and product safety for predominantly small beverage producing companies. With the change of name from Laboratory Romeis to Institute Romeis, Peter Romeis, managing partner, and Ingrid Schmittnägel, managing director, wanted to allow for the expanded business activities with analysis, consulting, service and pilot brewery. One more reason for Brauwelt to talk to both about the general direction of the institute and about its business activities.
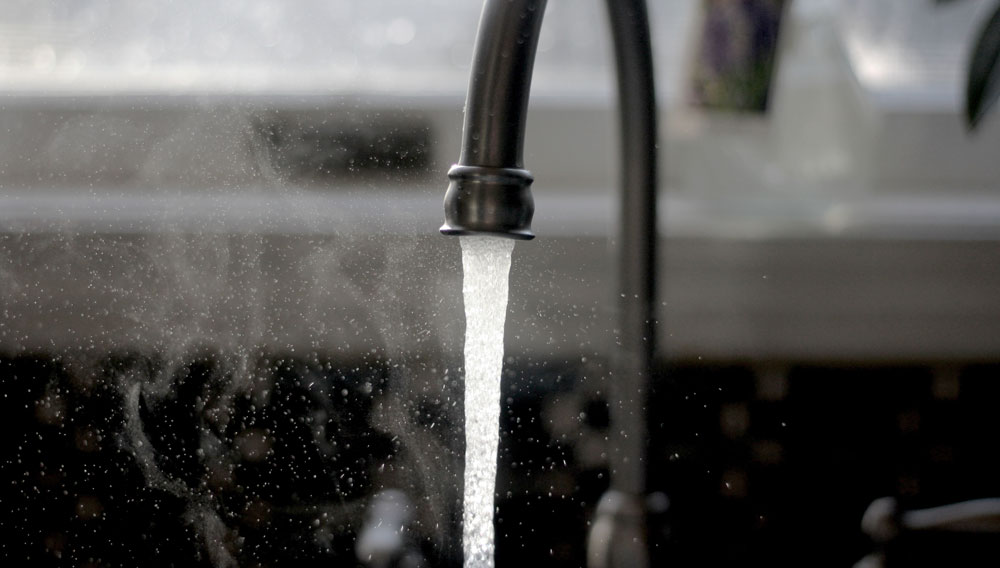
The use of vacuum pumps in the brewing industry for bottling beer is daily practice. Up to now, the standard has been the classic water ring pump. With the Eco vacuum pump, KHS is launching a new generation of pumps that offers considerable advantages. The decisive point is that this new pump concept reduces water consumption considerably thereby cutting operation cost noticeably.
Since half a year the Brasseries Kronenbourg in Obernai in the vicinity of Strasbourg runs one of the biggest reverse osmosis facilities for brewing liquor treatment in Europe. In close cooperation with the technical planning staff of Kronenbourg and the engineering consultants of Cical the Grünbeck Wasseraufbereitung GmbH in Höchstädt/Danube, Germany, planned, built and installed the new central water treatment facility with a permeate rate of 380 m3/h.
After successfully optimizing the lautering and boiling process with Pegasus, Merlin and Stromboli, the last major technological challenge in the brewhouse has been solved. By the Steinecker ShakesBeer Krones offers a completely new mashing technique which increases the quality of the mash, lowers the energy consumption and reduces the mashing time to under two hours. This makes 12 brews a day a reality in every brewhouse
Already 90 million closures have been decontaminated in a leading Swiss mineral water plant via dry process. The succeeding article compares the benefits of dry decontamination with other germ removing procedures on the basis of practical experience values.
According to information from the German Association of Natural Mineral Water Springs (Verband Deutscher Mineralbrunnen) the per capita consumption of mineral and spa water reached 113.7 l in Germany in the year 2002. The trend to mineral water without CO2 continued (+78.4 %). The all-time summer of 2003 yielded in more growth in which the market share of spa water again showed an increase above average. The method was filed for patent ...
One of the lecture blocks at the 91st Working Symposium of the VLB in Berlin dealt with the highly topical subject of "Beer in plastic bottles".
Alexander Buechler, PETplanet Publisher GmbH, Heidelberg/Germany, gave an up-to-the-minute review of this topic, stating that discounters are contributing to the acceptance of beer in PET. The table below provides an overview of the present status of beer in PET in Ger-many.
The listing shows that both monolayer and multilayer bottles are on the market. The choice of bottle material has a major influence on beer shelf-life. Monolayers without coating, as used by Darguner Brewery, lead to the worst values. Martens work with coating. Costs are therefore similar. Martens use a 28 g bottle, yet another cost advantage.e.....
The water degassing plant described below has been installed as one option to reduce the negative effects that oxygen has in brewing liquor, with a view to obtaining commercial, technological and qualitative advantages in filtration and filling.
Carbon dioxide (CO2) is used for degassing in the compact column, dispensing with expensive vacuum and multi-stage systems. The high degree of oxygen reduction to a residual oxygen content of less than 0.02 ppm comes about from desorption under atmospheric pressure with gaseous carbon dioxide (CO2).
Function
Mass transfer in the deaeration column is driven by the difference in solubility of oxygen or air and carbon dioxide gas, with contact over a very large reaction surface area. It then flows e.g.....
For many years, it has been widely accepted to blend deaerated water into a strong brew achieving a desired taste and alcohol level and a higher output rate without major changes in the brewhouse and cold block. This process is called High Gravity Brewing (HGB).
After adjusting the gravity by means of deserted water, sometimes called brewing liquor, the beer needs to be carbonated. The three processes, deaeration, blending and carbonisation can now be found in one process unit offered by Alfa Laval.
The ongoing globalisation and heavy competition in the brewing industry forces changes in the classical brewing process and requires adaptation of new process equipment and technology. This process is called High Gravity Brewing (HGB).....
The importance of water in transmission of certain infectious diseases is well established. A multiplicity of diseases, in particular those of the gastrointestinal tract, can be transmitted by drinking water. These are mainly diseases like typhoid, paratyphoid, cholera, cholerine, shigellosis, leptospirosis, verminosis, as well as diseases caused by viruses, such as e.g. hepatitis and poliomyelitis.
As a consequence of worldwide tourism and resulting contacts with potential epidemic areas, our drinking water is endangered in terms of epidemic hygiene at all times.
The objective of drinking water disinfection is to kill off pathogenic bacteria and to inactivate pathogenic viruses. Table 1 gives a summary of these disinfectants.e.g. by traces of heavy metals.