Long partnership | Molson Coors is one of the biggest brewery groups in the world. The Serbian plant run by its subsidiary Apatinska Pivara Apatin has relied on technology engineered by KHS for over four decades. The long and trusting partnership between the two companies was recently further cemented by conversions to two of the brewery’s glass lines and the procurement of a KHS Innofill Can DVD can filler. As a result of these extensive modernization measures, Apatin Brewery has been able to greatly optimize its line efficiency and product quality. The traditional brewery also benefits from improved hygiene and savings in energy and media.
Concentrated impurities | Modern machines for washing bottles, with their combination of chemical, thermal and mechanical cleaning functions, ensure that containers are cleaned properly. Nevertheless, the introduction of organic and inorganic impurities into the cleaning solution derived from adhesives and labels often presents special challenges. Caustic filtration and filtration of liquid in the water zone can offer more security in achieving the desired cleaning effect.
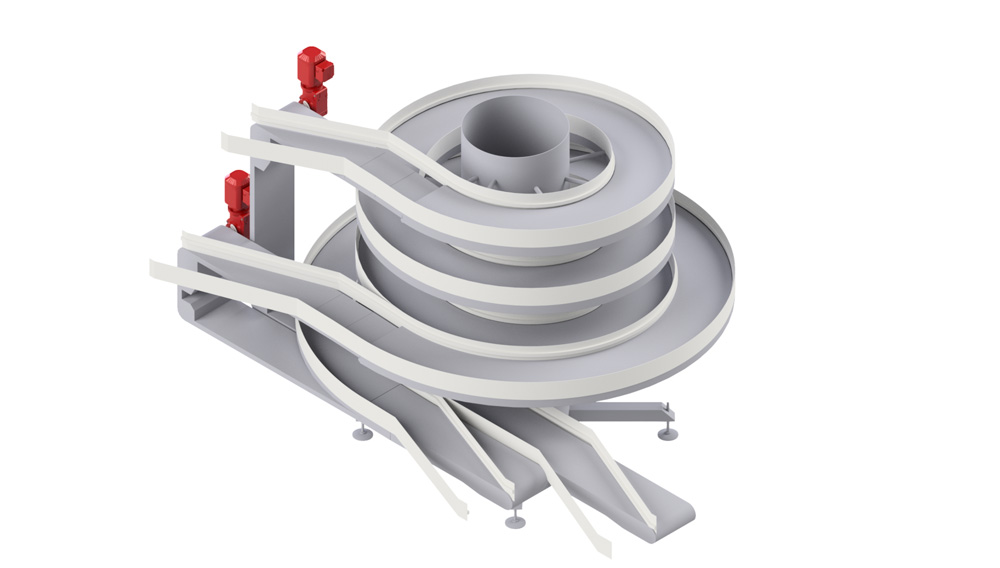
Taking things to a new level | The demands made of a line layout have dramatically changed over the years. The amount of space available is now one of the most important factors when designing a new line or expanding an existing setup. Free access areas for safe and cost-efficient maintenance are also essential. The creation and use of new levels is one good way of making the best and most cost-efficient use of the available space.
Large-scale project | Cutting-edge filling equipment, environmentally-friendly packaging and ambitious sustainability targets: Carlsberg is one of the beverage industry’s technological pioneers. The KHS Group consistently supports the brewery in the concrete implementation of its strategies. A number of projects have recently been successfully realized in China – including the installation of two canning lines. The focus here was on a streamlined layout and production design that are to act as a role model for all of the company’s Chinese factories.
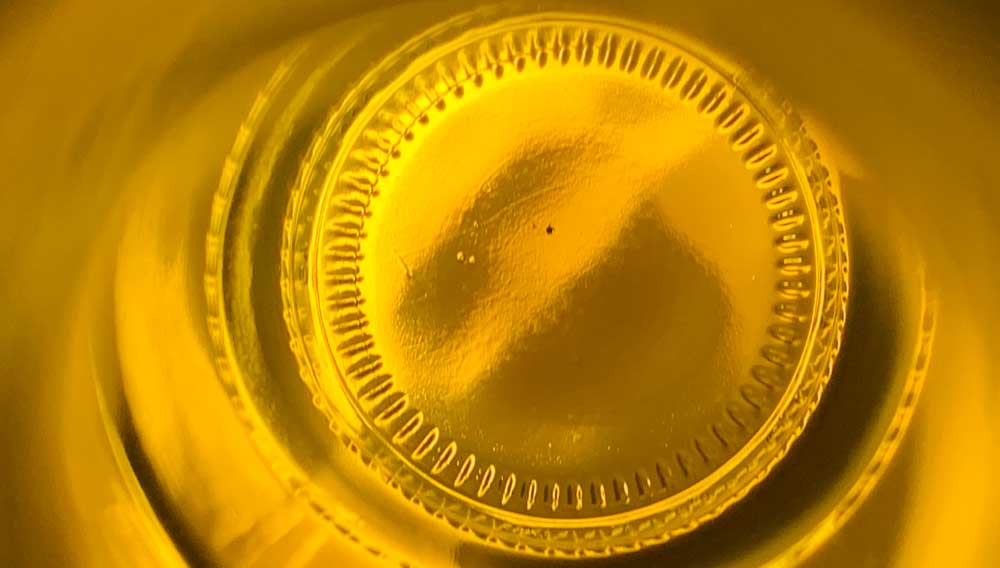
Inspection of empties | Regular verification of cleaning performance of bottle washers in breweries is important in order to ensure perfect product quality and product safety. This is the reason why the Research Center Weihenstephan for Brewing and Food Quality, Freising, Germany, in cooperation with five breweries, validated a test series with standardised contaminated bottles. This should enable breweries to carry out their own checks.
Dry preform sterilization | Nongfu Spring’s latest additions to its beverage portfolio required a hyper-flexible and safe aseptic solution, able to process high- and low-acid, still and carbonated products in PET, while enabling impactful bottle designs. With four decades of supporting sensitive beverage producers worldwide, Sidel recently engineered and installed a complete aseptic packaging line, integrating the Versatile Aseptic Combi Predis™. The line helped the leading Chinese beverage player launch a breakthrough in the domestic market: sparkling Ready-to-Drink (RTD) products, aseptically bottled in PET.
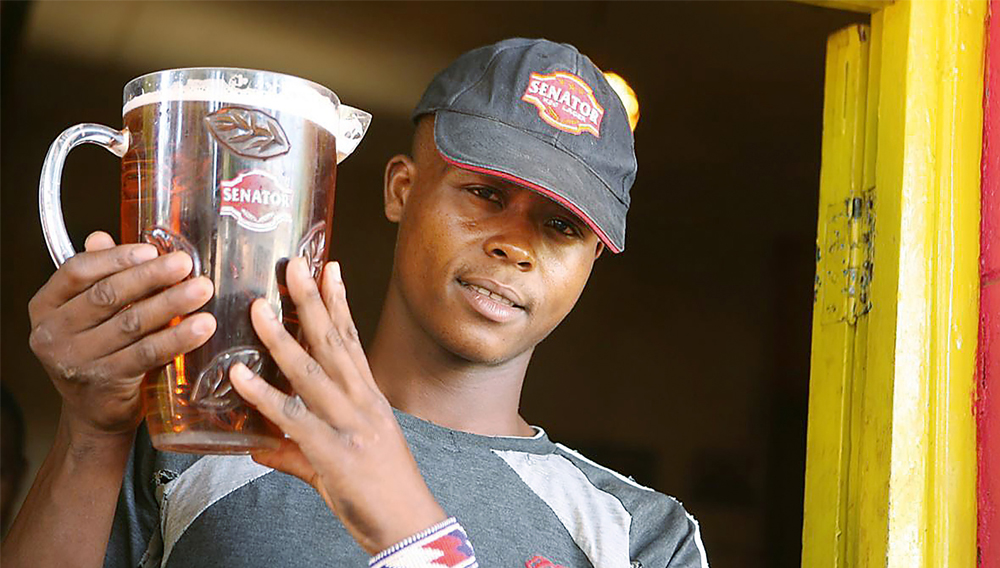
Proven partnership | The example of beer brand Senator Keg shows how you can effectively leverage market potential while exercising social responsibility. In Kenya this has proved successful with a clever strategy – and with the help of technology and service from KHS.
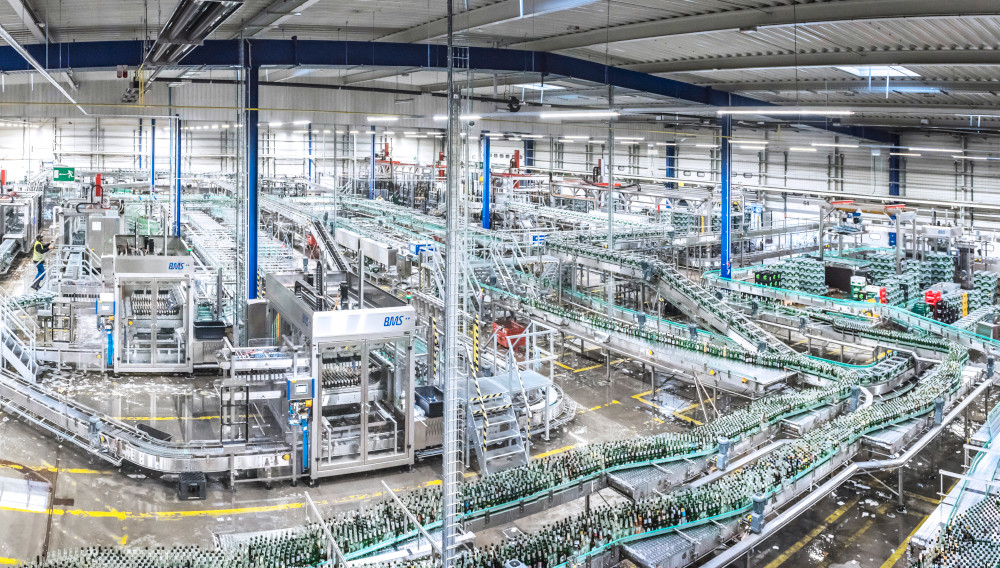
Mammoth project | In 2019 one of the most powerful and complex sorting systems in Europe went into operation in Bremen, Germany. With a rated output of 4500 crates per hour and seven sorting streams in an area of around 3000 m2, it was a mammoth project for BMS Maschinenfabrik GmbH from Pfatter, also in Germany.
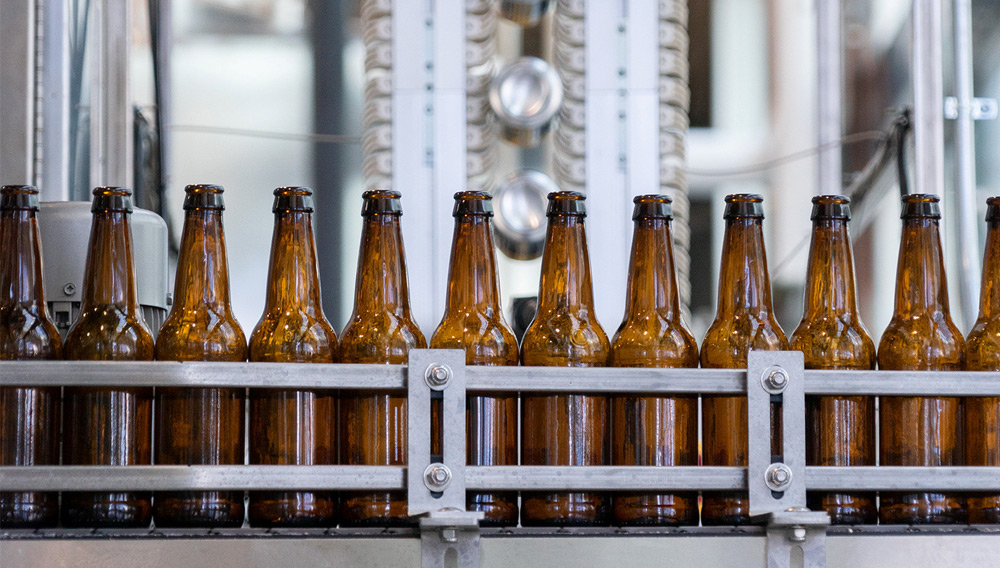
Quality products | People like Jim McCabe, founder of Milwaukee (MKE) Brewing Company, Milwaukee, WI, USA, are helping to ensure that Milwaukee is also associated with handcrafted beers. His model for success is to provide quality products with a local character made at a traditional location, using filling technology by KHS.
Sidel | Varun Beverages Ltd, Gurgaon, India, part of RJ Corp group, one of the largest franchises for PepsiCo Inc. globally, has installed Sidel’s Aseptic Combi Predis™ in its newly established plant in Punjab, India.
Flexibility | For Carlow Brewing Company GEA Vipoll, Križevci pri Ljutomeru, Slovenia, will install Ireland's first Visitron All-in-one line. Looking for a multifunctional filling system, the craft brewer chose GEA's combined rinser-filler-seamer block, which offers brewers maximum production flexibility and reliability.