Adequate solutions | As beer alternatives with low alcohol concentration or completely without alcohol are becoming increasingly popular worldwide, equipment manufacturers aim to provide their customers with adequate solutions, which take into account the importance of the raised hygienic conditions for these types of drinks.
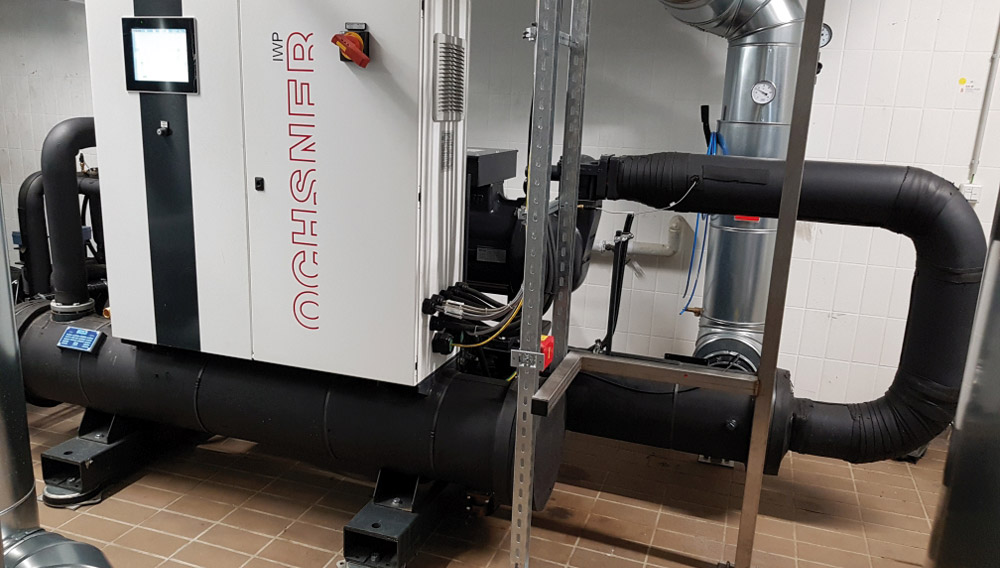
Field test | In spring 2019, the Bavarian brewery Aying Franz Inselkammer KG, Aying, commissioned a newly developed process combining a bottle washing machine (BWM) with a high-temperature heat pump (HTHP) and the existing co-generation plant (CGP).
Aseptically packed | Niche Cocoa Industry Ltd., Ghana’s largest fully integrated cocoa processor, recently signed a deal with Sidel with the intention to advance into previously uncharted territory: beverage production. The company are planning to support Ghana’s School Feeding Programme by providing 5.6 million pupils with ready-to-drink (RTD) chocolate milk, aseptically packaged in 250 ml PET bottles, for 100 school days per year.
Agr International, Inc | Automated Blowmolder Control systems take the guesswork out of the blowing process.
Global Data | Small scale breweries could run short of CO2 due to a significant shortfall of the production of this gas caused by the struggling oil industry.
Corona crisis | In the fight against COVID-19, Sidel have transformed their international centre of excellence for PET packaging development and blowing solutions in France into a production centre and launched an exceptional production of bottles for hydro-alcoholic gel.
Krones | The Contipure AseptBloc DN at the Austrian food and beverage producer Spitz uses gaseous hydrogen peroxide for sterilisation, and can handle 24,000 containers per hour.
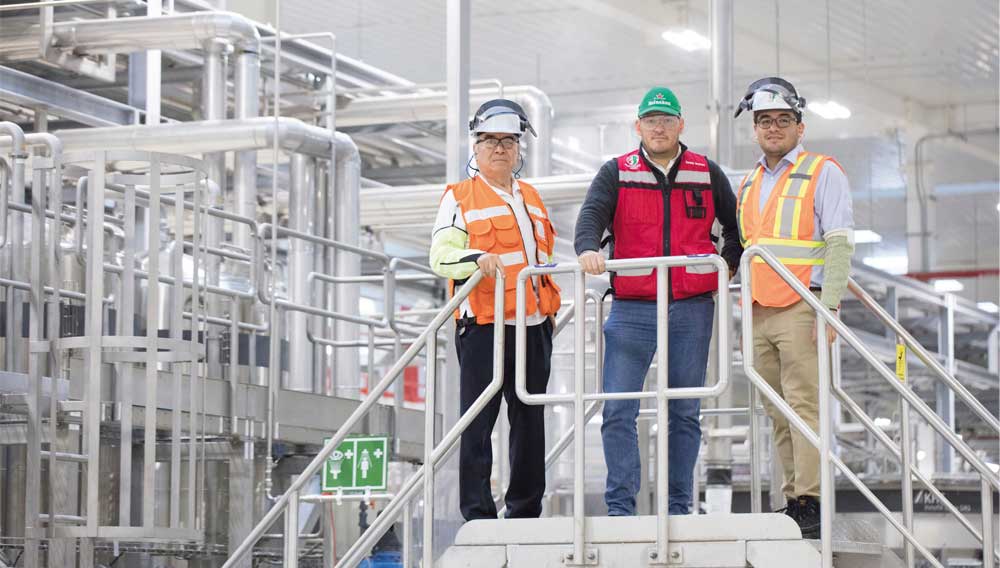
An exemplary plant | Heineken and KHS are setting standards with the newest and one of the biggest breweries in Mexico on all counts: besides its impressive proportions the plant is also a shining example when it comes to ecological and economic sustainability.
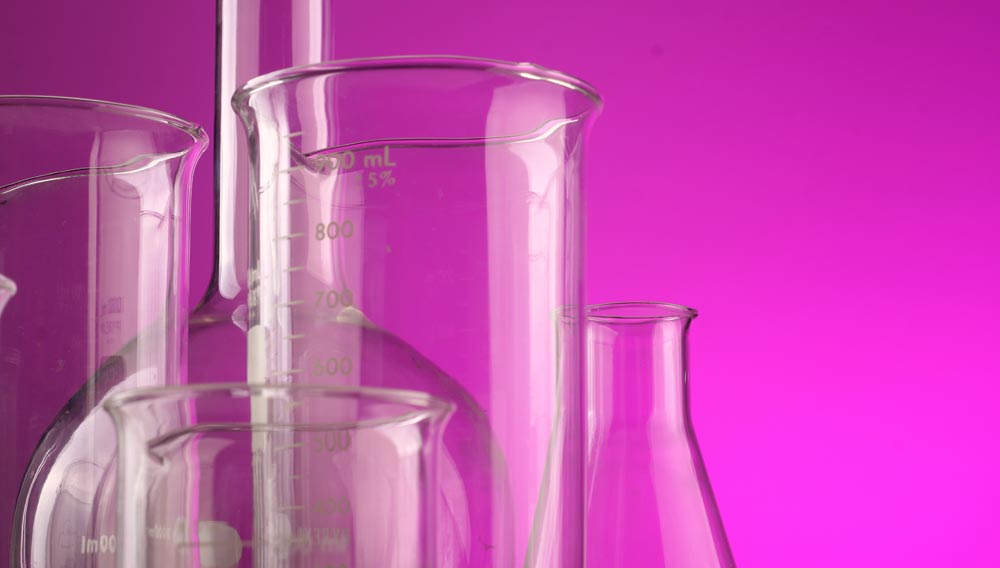
Focus on brewers’ yeast | Microbiological detection of foreign yeasts in the brewing process is an important part of hygiene monitoring in breweries. A novel DNA extraction and Real-Time PCR process might help here. This process can reliably detect S. cerevisiae var. diastaticus contamination, without previous enrichment.
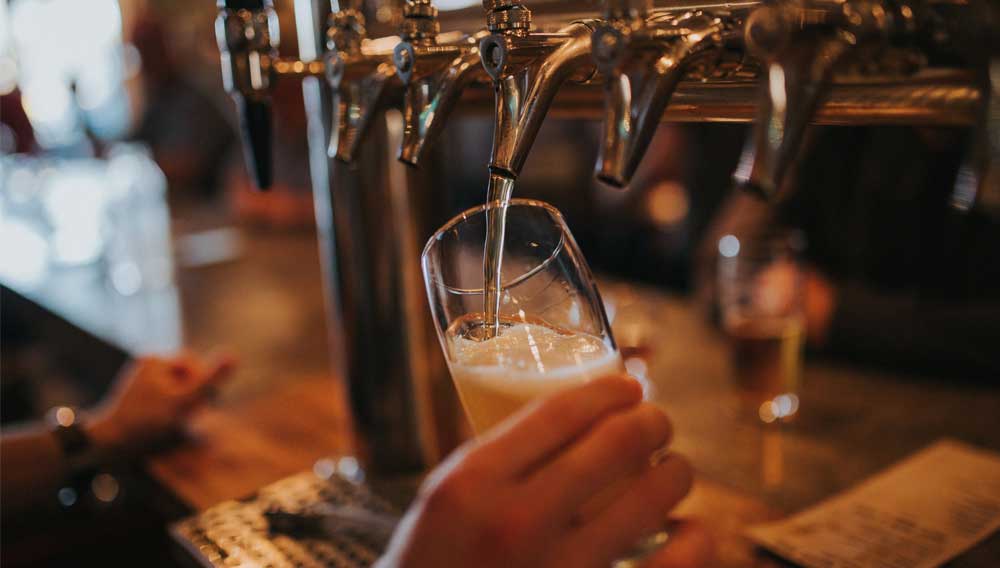
Cradle to cradle | Businesses around the world are under pressure to operate as sustainably as possible and the global brewing industry is no exception. Understandably, the use of packaging is under the spotlight in terms of supply chain benefits, product protection and with the rise in consumer environmental awareness the packaging end of life and re-use. Reduction in the use of plastics, recycling, was the aim a few years ago but now business models need to move towards a full circular evidenced lifecycle solution.
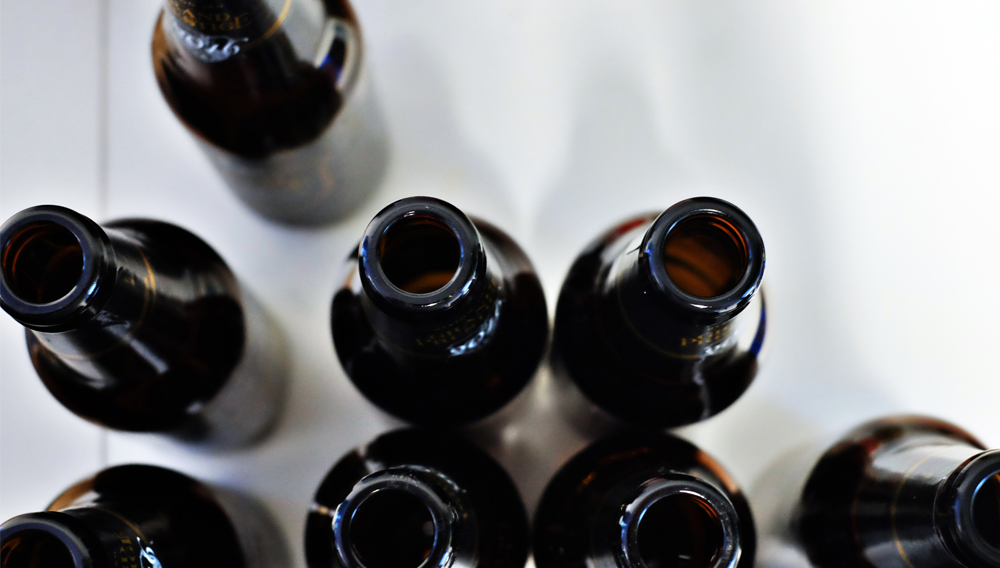
Patent pending | In this article, a new process for washing returnable bottles – patent pending – is presented. In terms of energy and water savings, it can be viewed as another quantum leap. Data is based on simulations of the manufacturer’s mechanical engineers and calculations of the inventor. The innovative process makes use of a combination of a bottle washing machine (BWM) combined with a high-temperature heat pump (HTHP) and integration into an (existing) cogeneration plant.