Water crisis | A few weeks ago marked the tenth anniversary of the financial crisis that sparked a sharp escalation in the cost of credit for banks, created a panic in financial markets, and led directly to all the other tumultuous events of the following year that cost tens of billions of euros. Much has since been written about the crisis of 2007 and whether lessons have been learned. Why were so many early warning signs ignored? One of the key learnings is a renewed focus on “stress testing”.
Water Degasification 2.0 | Degasification has become a widely established process unit operation for water treatment in the brewing and beverage industry. Depending on the particular industrial sector and use of degassed water, residual oxygen levels below 10 ppb are required. Use of a stripping gas, mainly CO2, in rare cases N2, is usual practice in all processes generally used in the beverage industry. Thanks to a new technology developed by corosys, no stripping gas and no thermal energy or chemicals are required. According to the company, the same low residual oxygen concentrations as in the most effective conventional processes are achieved.
Experience over a five-year period of full throughput using anaerobic co-digestion of brewery yeast for biogas production is described in this contribution. The brewery, with a total amount of available yeast (0.7 v/v %), had a 26.2 % increase in COD load and a 38.5 % increase in biogas production resulting in an increase in the biomethane/natural gas substitution ratio in the brewery from 10 % to 16 %.
Backus y Johnston is the largest brewing group in Peru with breweries in Lima (Ate), Chiclayo (Motupe), Arequipa, Cusco and Pucallpa. Well-known brands such as Cusqueña, Arequipeña or Pilsen Callao belong to the Group’s portfolio as well as soft drinks and mineral waters including San Mateo products. These brands, well-known beyond the borders of Peru, owe their success to consistent excellent quality that is ensured and continuously monitored with state of the art technology.
Many different technical solutions for improving the environmental performance in a brewery are widely available from the major brewhouse suppliers. In part 1 of this series, the combination of a vapour condenser, condensate cooler, heat storage tank (stratification tank) and wort preheater was discussed. This is the obvious choice for any new brewery for recovery and reuse of thermal energy, even though this solution is not always a guarantee that energy is effectively recovered and reused. Often there is an imbalance between heat recovery and heat reuse. In spite of the benefits, surprisingly few breweries use stratification tanks.
Energy-conscious brewing | Energy efficient practices in microbreweries and brewpubs reach a limit very rapidly due to the small volumes they produce. After a batch is brewed, a volume of hot brewing liquor correspondent to that of the cast-out wort is generated through the process of wort chilling, for which there is no practical use. This is where the principles of low-energy brewing can be applied. The brewing equipment is heated using a buffer tank filled with hot water from the heating system, and at the end of the brewing process, all of the thermal energy is returned to the heating system, where it can be utilized for other heating purposes.
With the Filtech Show taking place from 24-26 February 2015 the City of Cologne in Germany will turn into a meeting place for all those involved with filtration and separation and adjacent sectors.
The brewing process is inherently energy and water intensive. In the second part of this publication, the process parameters that affect environmental performance in the brewhouse and cellar sections are analysed in order to provide brewers with some guidance when they evaluate proposals for energy and water saving projects. The boiler house, cooling equipment and water treatment units are not included in this study because these topics are extensively covered already in other publications.
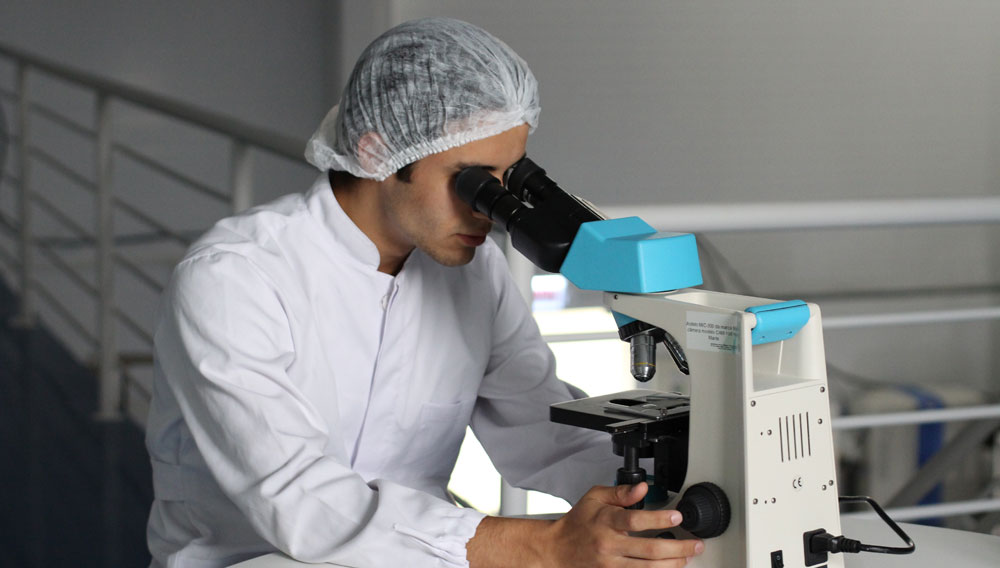
All over the world, manufacturers are under increasing pressure to manage natural resources in a responsible manner. This applies also to the brewing industry. Since most processes in a brewery are carried out batch-wise, energy and water recovery and reuse in a brewery is complicated though this is becoming more widespread now. In this first part of the publication, the brewhouse and cellar processes are mapped with the aim of calculating real brewery requirements for heating, cooling and fresh water usage in each step of the process. This flow sheet can then be optimised to lower overall water and energy consumption.
The 11th “Trends in Brewing” symposium is planned for April 13-17, 2014 and this year’s slogan is “Can Trends in Brewing be Revolutionary?” Organizers KAHO Sint-Lieven (KU Leuven), Ghent/Belgium, Heriot-Watt University, Edinburgh/UK, and the TU Berlin are hoping to recreate the resounding success of the previous event this year as well. The “trends” presented at the 2012 symposium attracted 360 industry representatives from a total of 24 nations to Flanders, where they met to discuss developments in brewing and malting technology.
BRAUWELT International congratulates Prof. Ing. Gabriela Basařová, DrSc. on her 80th birthday. Basařová was born on January 17, 1934 in Plzeň to a family of teachers. She graduated from secondary school in Plzeň and Institute of Chemical Technology in Prague, where she studied malting and beer brewing at the Department of Fermentation Chemistry and Technology. After graduating in 1957, she joined Plzeňské Pivovary, where she headed the control and research laboratories.
With the Eco vacuum pump KHS can already help the brewing industry to save almost 100 % water compared to the classic water ring pump. The new KHS Eco+ vacuum pump – or rather, the newly designed KHS Eco+ module integrated into the Eco vacuum pump – now has the added benefit that classic coolants for water recooling are now a thing of the past. This means that customers no longer have to invest in piping for coolant transfer which is often complex and costly.