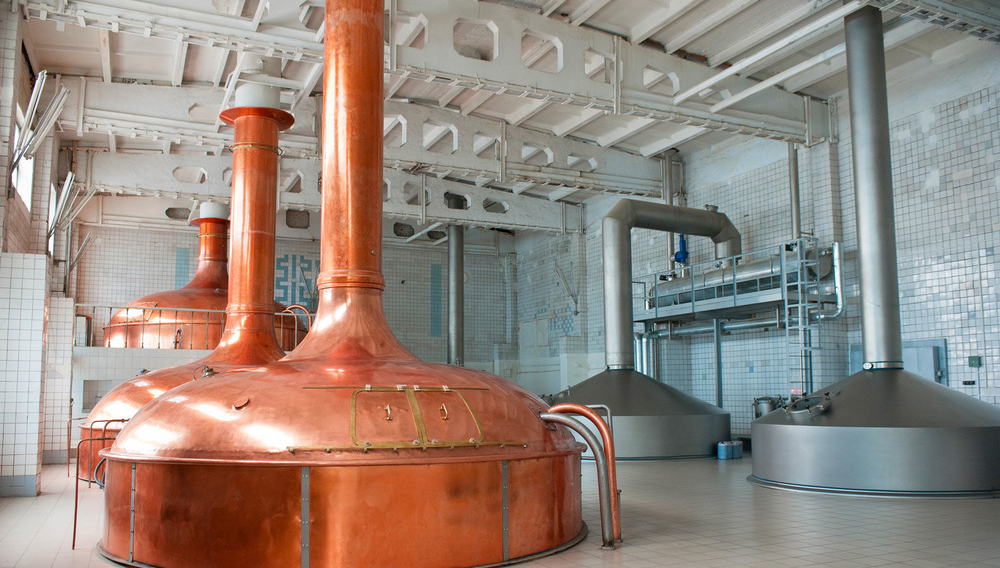
Hop-based inhibitory power | Hops as raw material contribute significantly to microbiological stability of beer. In the present contribution, determination of a so-called hop-based inhibitory power is described in order to assess the antimicrobial potential of beer. This will be verified in Part 2 based on commercial-scale tests.
Laboratory tests | It is generally known that hops are able to do much more than provide beer with bitterness, aroma and microbiological stability. To-date, the focus was on yield of bitter substances and hop aroma. However, no systematic research exists about the influence of hop addition and time of addition on oxidative beer stability. A research project at the Department of Brewing Science of the Technical University (TU) Berlin (AiF 17439) was devoted to resolving this issue.
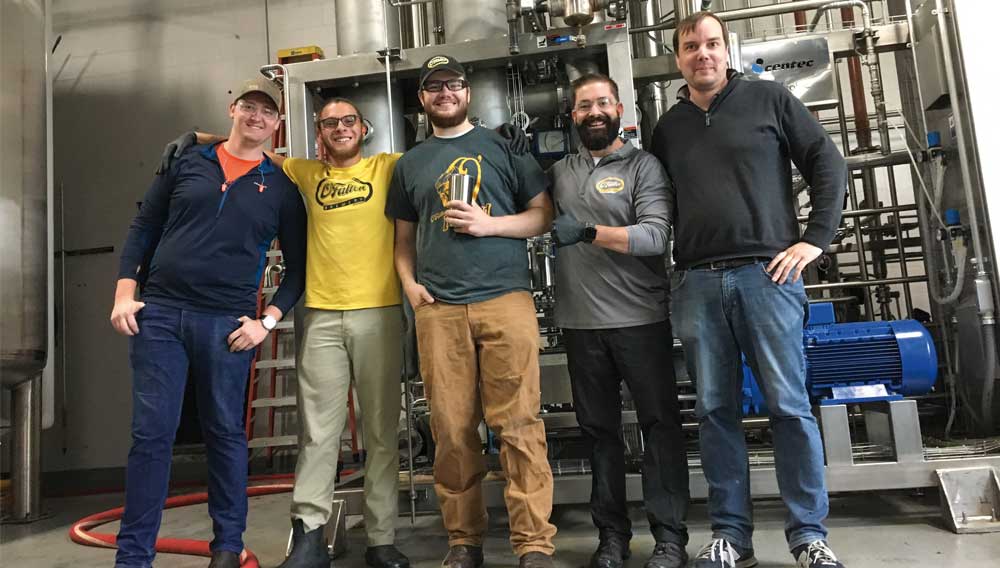
Brew well to be well | For many, beer is that must-have drink for the weekend and that small antidote after a stressful day. However, for Jeff Stevens, the relationship between himself and alcohol would never find common ground. In January 2017, Jeff left the world of alcoholic beverages and founded the Wellbeing Brewing Company in Maryland Heights, USA.

Beer as a cooling medium | After the first two parts (BRAUWELT International No. 5, 2018, pp. 345-349 and No. 6, 2018, pp. 426-429) have illustrated that an energy-self-sufficient and CO2-neutral brewery can already be translated into hands-on reality today, using tried-and-tested technology, the last part is intended to present in more detail two specifically selected, innovative components, without which the Brewnomic concept would be impossible to implement.
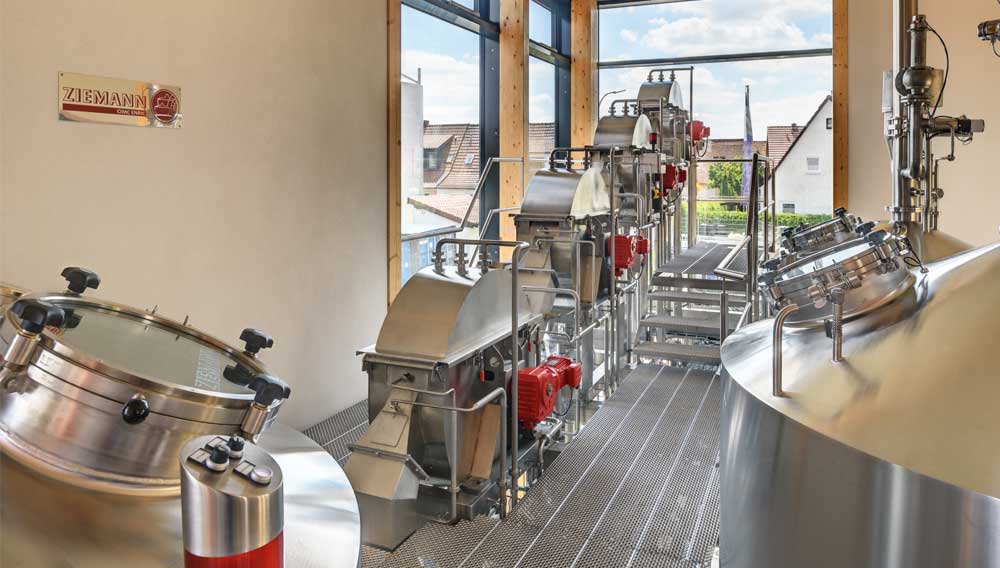
Trailblazer | Ziemann Holvrieka GmbH from Ludwigsburg has developed a revolutionary process for mash filtration with Nessie by Ziemann. At the same time, it opens the door to a completely novel process for wort preparation. The Omnium by Ziemann brewing process, celebrating its world premiere at drinktec 2017 and installed in a new brewhouse for the first time, is the result of an interdisciplinary research and development project. The medium-sized Schlossbrauerei Reckendorf in Franconia is at the forefront. This article provides a technical portrait and first results.
Alternative | The market for gluten-free food is growing contin-ually, up 25 per cent in 2015 alone. Several methods are well-established for producing gluten-free beer. However, most methods are detrimental to the brewing process, product quality and legislation. Use of malt enzymes may be a potential alternative.
Energetic optimisation | The first part of this article (BRAUWELT International No. 5, 2018, pp. 345-349) discussed the question of what kind of process design is the most suitable one for a brewery. In conclusion, clear advantages of the batch process over continuous process variants were found.
The Neutraubling-based manufacturer of filling and packaging solutions has acquired MHT Holding AG (MHT). MHT, based in Hochheim, Germany, together with its subsidiaries is providing injecting molding tools and services to the PET industry. The company generates approximately EUR 25 million revenues with 125 employees.
Based on the result of the first nine months of 2018 and the forecast for the fourth quarter, Krones reduces its turnover and earnings forecast. Due to rising costs of goods and labour, start-up expenses and one-time costs for the expansion of the global footprint, the Neutraubling-based company now expects an operative EBT margin of approximately 6.5% which is adjusted for the one-time expenses. The previous target was 7%.
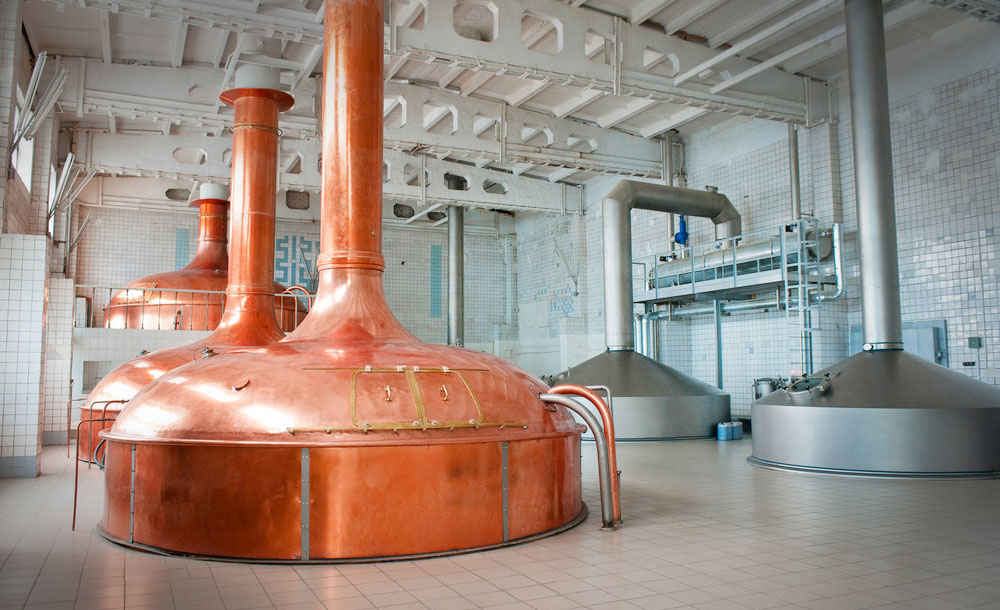
View into the future | Modern-day brewers are just as aware of their craft’s time-honoured traditions as they are receptive to new processes and techniques, which serve to either improve the quality of their beloved beer or help to reduce the costs of making it. So any changes are subjected to meticulous scrutiny before a decision is taken to strike out in a new direction.
Multi-functional | When designing small breweries, proven systems installed in large breweries are usually downsized. The patented brewhouse concept described in this article takes a different approach to design a simple, flexible and efficient system for brewhouse sizes from about five to 50 hectolitres/brew.