Corona crisis | To support the global response to this crisis, the Tetra Laval Group , Pully, Switzerland, will donate 10 Mio EUR to various voluntary organisations supporting the health care systems across the countries that we operate in.
Corona crisis | The Carlsberg Foundation, the New Carlsberg Foundation and the Tuborg Foundation are targeting extraordinary grants that can mobilize and support researchers, art museums and civil society in the scientific, economic and human efforts at a time when society is challenged by the COVID-19 epidemic.
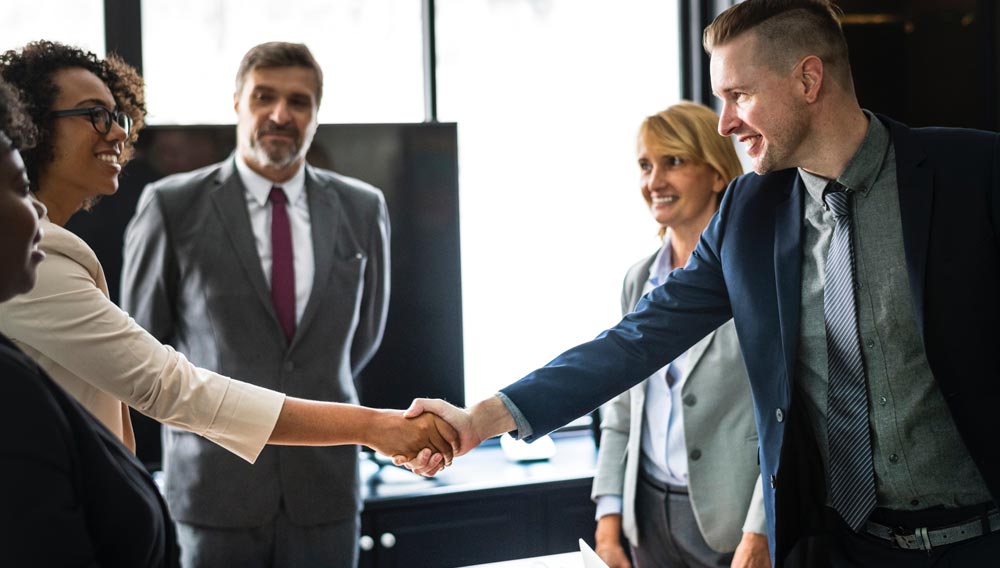
Employer attractiveness | How can medium-sized breweries succeed in competing for top performers with passion for their brewery and commitment in the recruiting process? For this, particular employer attractiveness and a well-organized recruiting and onboarding process are important.
Complexity is manageable | Digitalization is the buzzword these days in the media. Digital transformation can no longer be halted and brings with it new opportunities for the future. However, concrete applications and tangible evidence of its implementation are not easy to identify. Consequently, it is not surprising that the brewing and beverage industry exhibits a certain degree of reluctance to embrace it unconditionally.

Ideas for the future | Industry pioneers such as Lorenz Adalbert Enzinger and Theo Seitz bear witness to the long tradition research and development enjoys at KHS. Like them today’s KHS engineers don’t always go with the flow but pursue many different paths in order to stay at the helm of progress. The article describes how KHS GmbH from Dortmund deals with digitization and other topics of the future and prepares for it.
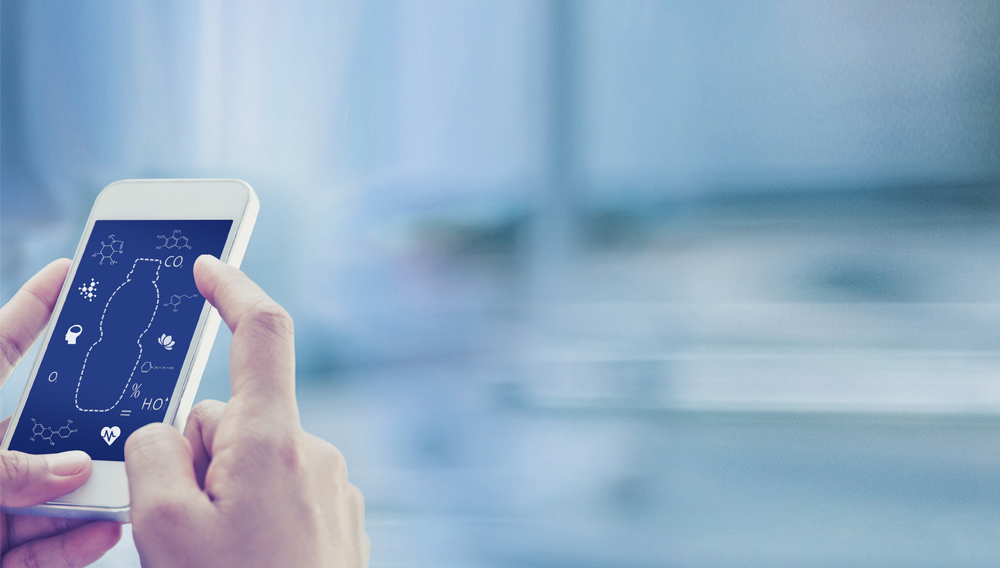
A rapidly growing world population, progressive digitalisation and the trend of individualisation represent serious challenges that the food industry and their ingredient suppliers are facing. However, these challenges also provide big opportunities as Marco Schmidt, CTO of Doehler GmbH, Darmstadt, Germany, pointed out as part of a talk on the topic of “innovation” at drinktec.
Continuous improvement | While growth in craft breweries maintains to outpace that of the brewing industry, there is a increasing need to identify practical ways to help drive operational performance. Improved operational performance can include enhanced product quality, product safety, higher yields and lower costs, and increased capacity without the need for additional capital. These goals are very doable if one starts by focusing on the most important metrics first, and has an effective way to drive improvement on those metrics.
That backfired. At AB-InBev’s AGM on 26 April 2017, a representative from NN, a large Dutch insurer, complained to AB-InBev’s board that at AB-InBev “we see little diversity, insufficiently independent directors and especially a bonus culture for employees and managers that are not in line with international standards.”
Processes in the beverage industry place unique demands on conveyor systems and their drives, where all of the movement and the various speeds are determined by the filling process. As breweries update their equipment, many are turning to SEW-Eurodrive for energy-efficient mechatronic drives with a focus on hygienic design.